Delivering Excellence: A Success Story in SMT Production
In the world of nuclear instrumentation, precision and reliability are paramount. One of the leading manufacturers of nuclear detection devices in the United States faced the challenge of producing high-precision products that demanded reliable quality and frequent updates. They needed a partner capable of delivering customized portable PCBs and surface mount assembly (SMT) services to meet their unique requirements. In this blog, we present a real-world case study of how WINOW, a top-tier PCB assembly manufacturer, successfully collaborated with the customer to achieve outstanding results.smt production.
What’s SMT Production?
1. The Foundations of SMT Technology
At its core, SMT Production involves mounting electronic components directly onto the surface of a printed circuit board (PCB) instead of passing leads through holes. This process eliminates the need for bulky through-hole components, resulting in reduced weight, smaller form factors, and enhanced electrical performance.
2. State-of-the-Art Machinery and Technology
WINOW takes pride in its cutting-edge manufacturing equipment and technology that propels its SMT production to new heights. Advanced pick-and-place machines with high-speed, precision nozzles meticulously position components onto the PCB, ensuring an impeccable connection. Automated optical inspection (AOI) systems further verify the placement accuracy, guaranteeing a defect-free assembly.
Understanding the Customer’s Needs
The customer’s focus on detecting, measuring, and analyzing low-level ionizing radiation required sophisticated electronic devices. This called for high-precision PCBs that could withstand demanding environmental conditions while maintaining consistent performance. Additionally, the customer required a quick turnaround and regular updates to improve their product offerings continually.
Providing Professional Design Support
From the beginning of the collaboration, WINOW understood the significance of providing professional design support. Their experienced team worked closely with the customer to comprehend their specific requirements, ensuring a seamless transition from concept to production. By offering design suggestions and efficient team services early on, WINOW set the stage for a successful partnership.
Swift and Reliable Production
To meet tight deadlines, WINOW swiftly initiated the manufacturing process after receiving the customer’s drawings. Within just 2.5 weeks, the 4L FPC+SMT order was completed, showcasing WINOW’s commitment to timely delivery without compromising on quality.
Quality Assurance Measures
In a domain as critical as nuclear instrumentation, product quality cannot be compromised. To ensure the highest quality standards, WINOW performed rigorous AOI (Automated Optical Inspection), X-ray, and functional testing before shipment. These comprehensive quality assurance measures guaranteed that the delivered products met the strictest performance benchmarks, instilling confidence in the customer and end-users alike.
Customized Solutions
WINOW’s flexibility and expertise allowed them to provide customized SMT Production solutions tailored to the customer’s unique needs. They specialized in offering GSM board surface mount assembly services that catered to the specific requirements of the nuclear instrumentation industry. This level of customization played a pivotal role in the success of the project.
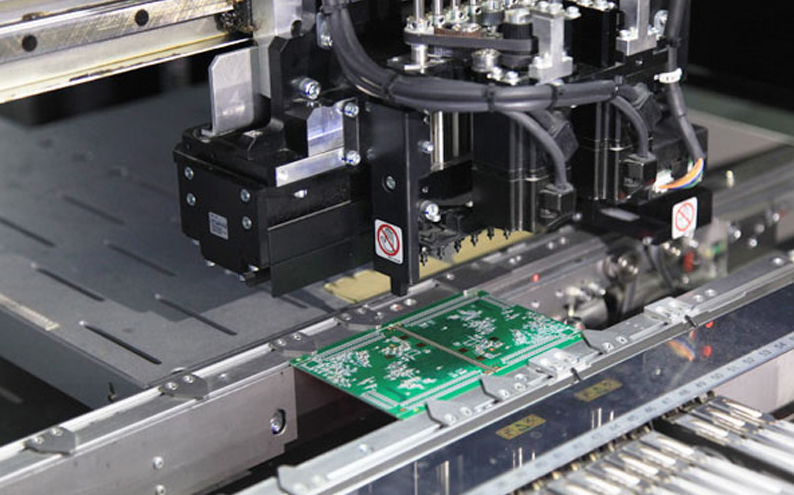
Benefits and Lessons Learned
The collaboration between the customer and WINOW yielded several benefits and valuable lessons:
1. Efficiency: By leveraging WINOW’s technical expertise and efficient team services, the customer experienced a streamlined manufacturing process, reducing time-to-market and overall project costs.
2. Quality Assurance: Rigorous testing and inspection processes ensured the delivered products were of the highest quality, meeting the stringent requirements of the nuclear instrumentation industry.
3. Flexibility: WINOW’s ability to adapt to changing project needs and provide customized solutions underscored its commitment to customer satisfaction.
4. Long-term Partnership: The successful completion of the project fostered a strong and long-term partnership between the customer and WINOW, setting the stage for future collaborations.
The SMT Production Process at WINOW
1. Prototyping and Design
Before full-scale production, WINOW’s team of skilled engineers collaborates with clients to create prototypes and optimize PCB layouts. This crucial stage ensures that all technical specifications are met, minimizing errors and reducing the time to market for new products.
2. Component Sourcing and Inspection
WINOW maintains strong partnerships with reputable suppliers to source top-quality components. Rigorous inspections are conducted to validate their authenticity and compliance with industry standards, ensuring the final products meet the highest quality requirements.
3. Solder Paste Stenciling
In this step, solder paste is precisely applied to the PCB through stencils. The stencil acts as a mask, depositing the paste onto the designated pads. The solder paste is essential for securely attaching the components during the subsequent soldering process.
4. Pick-and-Place Assembly
Here comes the magic of SMT production. WINOW’s high-speed pick-and-place machines swiftly and accurately place components onto the PCB using computer-controlled precision. The combination of speed and precision in this step is critical to achieving high yields and cost-effectiveness.
5. Reflow Soldering
After component placement, the PCBs move to the reflow soldering process. In this stage, the PCBs pass through a temperature-controlled oven, causing the solder paste to melt and creating secure electrical connections between the components and the PCB.
6. Inspection and Quality Assurance
Once the soldering is complete, each PCB undergoes thorough inspection using automated optical inspection (AOI) systems. These systems detect potential defects such as misaligned or missing components, soldering issues, and other anomalies, ensuring the highest level of quality control.
Quality Control: WINOW’s Hallmark
1. In-line Inspection
WINOW implements in-line inspection systems at various stages of production. Automated optical inspection (AOI) and X-ray inspection ensure that components are placed correctly, and solder connections are defect-free.
2. Functionality Testing
Before products leave the production line, WINOW conducts comprehensive functionality tests to verify that they meet the specified performance standards. This rigorous testing process minimizes the chances of faulty products reaching the end users.
3. Lead-Free Soldering
WINOW is committed to environmental sustainability and employs lead-free soldering in its SMT production process. This eco-friendly approach aligns with global efforts to reduce hazardous waste and promotes the production of environmentally responsible electronics.
4. Recycling Initiatives
To further its commitment to environmental preservation, WINOW implements recycling programs for waste materials generated during the SMT production process. This ensures responsible waste management and minimizes the impact on the environment.
Conclusion
The case study of WINOW’s collaboration with a prominent nuclear instrumentation manufacturer demonstrates the importance of professionalism, expertise, and customization in the field of SMT production. By delivering high-precision, customized PCBs with reliable quality and efficient services, WINOW showcased its capabilities as a top-tier SMT Production manufacturer. As technology continues to evolve, successful partnerships like this will play a critical role in advancing innovation and addressing the complex challenges of various industries.