The Secrets of PCB Solder Mask: Master Your Fabrication Process!
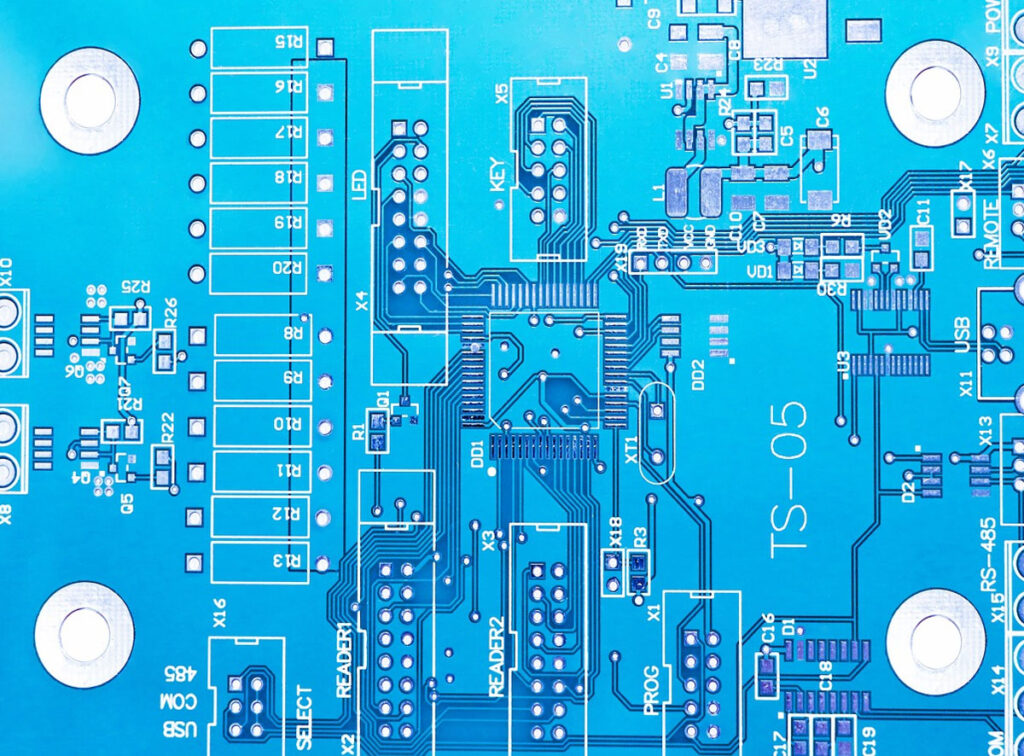
Are you looking to gain a better understanding of how to use PCB solder mask in your fabrication process? Solder mask is an important part of the printed circuit board (PCB) fabrication process and can greatly affect the performance and reliability of your board. In this blog, we’ll unlock the secrets of PCB solder mask, including its benefits, types, selection criteria, and application process. We’ll also cover helpful tips for applying solder mask and common challenges you may face. Read on to learn more about this essential part of the PCB fabrication process!
A PCB (printed circuit board) solder mask is a layer of protective coating that is applied to the surface of a PCB. The purpose of the solder mask is to insulate and protect the copper traces on the PCB from accidental shorting, as well as to prevent corrosion and damage to the PCB.
The solder mask is typically made of a polymer material, such as epoxy or polyimide, and is applied to the PCB using a silk screen printing process or a liquid photoimageable (LPI) process. After the solder mask is applied, it is cured using heat or UV light.
Solder mask is typically green in color, although it can also be found in other colors, such as blue, black, and red. The color of the solder mask is chosen to contrast with the color of the copper traces on the PCB, making it easier for the assembler to visually identify the different components and connections on the board.
In addition to providing protection and insulation, the solder mask also helps to improve the appearance of the PCB by covering up any blemishes or imperfections in the copper traces. This can be particularly important for PCBs that will be visible to the end user, such as in consumer electronics products.
What is a PCB Solder Mask?
A PCB solder mask is a protective layer that is applied over the copper traces on a PCB. It is a thin polymer coating that is used to insulate the copper traces and reduce the risk of shorts on the printed circuit board. Solder mask helps to protect the board from corrosion, dust, and other environmental contaminants. It also increases the board’s durability by providing an additional layer of protection.
The solder mask is typically applied to the board in the form of a liquid, which is then cured to form a solid coating. This coating can be either green or black in color, though other colors are available. The solder mask is then used to mask off the copper traces and any other components that should not be soldered. This ensures that only the areas that need to be soldered will be exposed.
Benefits of Using a PCB Solder Mask
There are several benefits to using a PCB solder mask in your fabrication process. The first is improved reliability. The solder mask helps to reduce the risk of shorts by preventing any stray solder from bridging two different copper traces. This can improve the durability and reliability of the board, as well as its lifespan.
The solder mask can also help to reduce the risk of corrosion. The coating provides an extra layer of protection to the copper traces, helping to reduce the risk of oxidation and other forms of corrosion. This can help to extend the life of the board and improve its performance.
The solder mask also provides a visual inspection tool. The mask can help to identify potential issues with the board, such as shorts and open circuits. This can help to ensure that the board is working correctly before it is soldered.
Types of PCB Solder Mask
There are several different types of solder mask available for PCB fabrication. The most common type is liquid photoimageable (LPI) solder mask. This type of mask is applied to the board in a liquid form and then cured to form a solid coating. It is a popular choice for its good adhesion and ability to produce a uniform coating.
Another type of solder mask is dry film solder mask. This type of mask is applied to the board in the form of a thin film that is then cured to form a solid coating. Dry film solder mask is a good choice for high-volume production runs, as it is more cost-effective than LPI solder mask.
Other types of solder mask include solder paste and thermal transfer solder mask. Solder paste is applied to the board in the form of a paste and then cured to form a solid coating. Thermal transfer solder mask is applied to the board in the form of a thin film that is heated in order to form a solid coating.
Selection Criteria for PCB Solder Mask
When selecting a solder mask for your PCB fabrication process, there are several factors that you should consider. First, you should consider the type of material that you are using. Different materials require different types of solder mask and some materials may require special coatings.
You should also consider the size of the board and the complexity of the circuit. Different boards require different types of solder mask and some circuits may require special coatings.
Finally, you should consider the environment in which the board will be used. Different environmental conditions may require different types of solder mask and some environments may require special coatings.
PCB Solder Mask Application Process
The application process for a PCB solder mask is relatively straightforward. The first step is to prepare the board by cleaning it and removing any contaminants. This helps to ensure that the solder mask will adhere properly to the board.
Next, the solder mask is applied to the board in the form of a liquid or thin film. The solder mask is then cured to form a solid coating. This process helps to ensure that the solder mask will adhere properly to the board and provide a uniform coating.
Once the solder mask has been applied and cured, it is time to inspect the board. This is done to ensure that the solder mask has been applied correctly and that there are no shorts or other issues with the board.
PCB Solder Mask Finishes
PCB solder mask is available in a variety of finishes. The most common finishes are matte, semi-gloss, and gloss. Matte finish solder masks are the most common and are used when a uniform coating is desired. Semi-gloss and gloss finishes are best used when a high-gloss finish is desired.
Tips for Applying PCB Solder Mask
When it comes to applying a PCB solder mask, there are a few tips that can help to ensure that the process goes smoothly. First, it’s important to ensure that the board is clean before applying the solder mask. This helps to ensure that the solder mask will adhere properly to the board.
It’s also important to ensure that the solder mask is applied in the correct thickness. Too thin a coating may not provide adequate protection to the board, while too thick a coating can lead to shorts and other issues.
Finally, it’s important to ensure that the solder mask is cured properly. This helps to ensure that the solder mask will adhere properly to the board and provide a uniform coating.
Challenges of PCB Solder Mask Application
There are a few challenges that can be encountered when applying a PCB solder mask. One of the most common challenges is the risk of shorts. If the solder mask is applied too thick, it can lead to shorts between two different copper traces. This can cause the board to fail or malfunction.
Another challenge is ensuring that the solder mask is cured properly. If the solder mask is not cured properly, it can lead to poor adhesion and a lack of uniformity in the coating. This can lead to a number of issues, including shorts and open circuits.
Finally, it’s important to be aware of any environmental conditions that may affect the solder mask. Certain environmental conditions, such as high humidity or temperature, can affect the adhesion of the solder mask and lead to a number of issues.
Troubleshooting PCB Solder Mask Issues
If you encounter any issues when applying a PCB solder mask, there are a few steps that you can take to troubleshoot the problem. First, it’s important to inspect the board for any signs of shorts or open circuits. This can help to identify the source of the problem.
If the board appears to be functioning correctly, it’s important to check the solder mask for any signs of poor adhesion or a lack of uniformity in the coating. If the solder mask appears to be uneven or not adhering properly, it may be necessary to re-apply the solder mask.
Finally, it’s important to check the environmental conditions in which the board is being used. Certain environmental conditions, such as high humidity or temperature, can affect the adhesion of the solder mask and lead to a number of issues.
PCB solder mask is an essential part of the PCB fabrication process. It helps to insulate the copper traces and reduce the risk of shorts, as well as protect the board from corrosion, dust, and other environmental contaminants. There are several types of solder mask available, each with its own benefits and drawbacks. When selecting a solder mask for your board, it’s important to consider the type of material being used, the size of the board, and the environment in which the board will be used. The application process for PCB solder mask is relatively straightforward, though there can be some challenges that arise. Finally, it’s important to be aware of any environmental conditions that may affect the solder mask, as well as any troubleshooting steps that can help to resolve any issues. Mastering the use of PCB solder mask can help to ensure that your board is reliable and performs as intended.