PCB Medical
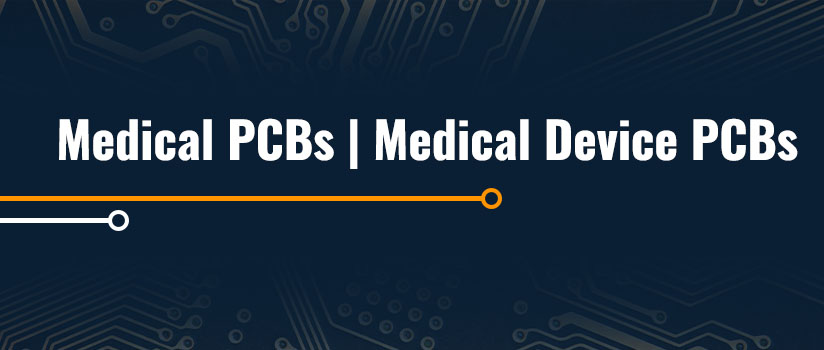
Winow New Energy Co.,ltd (winow) has been manufacturing custom-printed circuit boards for medical devices for more than 15 years. We’ve consistently ensured every board meets the highest quality standards for our customers, who include hospitals, clinics, and other healthcare professionals.
PCB stands for Printed Circuit Board, which is a board made of insulating material (such as fiberglass or plastic) with conductive pathways etched onto its surface. PCBs are used in a wide range of electronic devices, from computers to medical equipment.
In the context of medical devices, PCBs can be used to build a variety of electronic components such as sensors, controllers, and power supplies. Medical PCBs are designed to meet the specific requirements of medical devices, such as high reliability, accuracy, and safety.
Medical PCBs can be found in devices such as ultrasound machines, patient monitoring systems, X-ray machines, and medical imaging equipment. These devices often require high precision and accuracy in order to produce accurate and reliable results, which is why the PCBs used in medical devices are designed and manufactured to strict standards.
In addition, medical PCBs are subject to strict regulations and standards to ensure that they meet the highest levels of safety and quality. The manufacturing processes used to produce medical PCBs must adhere to strict guidelines to ensure that the final product is safe for use in medical settings.
PCBs for medical instrumentation are designed with precision in mind to meet the needs of your medical instrumentation needs and a wide range of care settings and lab settings. Precision is the core focus of our PCB fabrication services, and we always provide excellent results.
Challenges of the Medical Industry
Medical PCBs are designed to meet a number of requirements in order to ensure they deliver the performance required. A few primary challenges a PCB provider must be aware of when sourcing medical PCBs include ensuring their PCBs meet compliance standards, size and reliability standards. Review more information about these challenges below:
Medical PCBs are designed to meet the specific requirements of the medical industry, which includes compliance with regulatory standards such as the International Electrotechnical Commission (IEC) 60601-1 standard for medical electrical equipment. These standards ensure that medical PCBs are safe, reliable, and effective for use in medical settings.
Medical PCBs are used in a variety of medical devices such as:
- Patient monitoring devices such as an electrocardiogram (ECG) machines, blood pressure monitors, and pulse oximeters.
- Diagnostic imaging equipment such as ultrasound machines, X-ray machines, and MRI scanners.
- Therapeutic devices such as defibrillators, infusion pumps, and ventilators.
- Laboratory equipment such as analyzers and incubators.
In the medical industry, PCBs must meet strict quality and reliability standards to ensure that they operate effectively and safely. Manufacturers of medical PCBs typically use specialized materials and production processes to ensure that their products meet these standards.
Consider These Factors When Designing Medical Grade Pcbs.
Designing medical grade PCBs requires careful consideration of several important factors, including:
- Reliability: Medical devices are often critical for patient health and safety, so reliability is paramount. Medical grade PCBs must be designed with robust materials and manufacturing processes that can withstand harsh environments and repeated use.
- Performance: Medical devices must perform their intended functions with high accuracy and precision. PCBs should be designed to minimize noise, interference, and other sources of signal degradation to ensure accurate and reliable performance.
- Safety: Medical devices must be safe for patients and medical staff to use. PCBs must be designed to meet strict safety standards and regulations, including electrical safety, electromagnetic compatibility (EMC), and thermal management.
- Sterilization: Medical devices must be sterilized to prevent infection and ensure patient safety. PCBs must be designed with materials and coatings that can withstand various sterilization techniques, such as autoclaving, gamma irradiation, or chemical sterilization.
- Traceability: Medical devices must be traceable from manufacture to end-of-life disposal. PCBs should be designed with unique identifiers or barcodes to track and trace the device throughout its life cycle.
- Documentation: Medical device manufacturers must provide documentation of the PCB design, testing, and manufacturing processes to meet regulatory requirements. PCB designs should be well-documented with clear and concise specifications, testing procedures, and quality control measures.
- Cost: Medical device manufacturers must balance the need for high-quality, reliable PCBs with cost-effectiveness. PCB designs should optimize the use of materials and manufacturing processes to achieve the desired performance and safety requirements while minimizing cost.
OUR CAPABILITIES
We help medical device engineers and designers by providing complete PCB fabrication and engineering support for your products. Our ability to generate high-frequency, high-density interconnects can be applied to medical devices.
Get more info on how our PCB capabilities can help you go from concept to market below:
Prototyping: winow can help you with PCB prototypes to test the design and PCB prior to going into production.
Engineering support: Our team at winow provides engineering support services, consulting with our customers to ensure they get the best possible PCBs. Some of our most popular services include Design Rule Check, Design for Manufacturability, cost consulting, and stack up design, as well as surface finish consulting and laminate and raw material considerations. We can help you create PCBs that meet both your financial and quality needs.
Fabrication:We work with our customers to provide them with engineering solutions and prototypes, as well as oversight of the PCB manufacturing process. Since creating PCBs involves many steps, we have long-standing, strategic partnerships with domestic and overseas PCB facilities capable of providing high-quality products at an affordable rate.
Lifecycle:Once we’ve finished manufacturing your PCB, we can help you with any problems or issues that may arise. We’ll also help you manage revisions to the board if your product has any defects.