PCB Components Assembly Machine: Streamlining Your Manufacturing Process
A PCB components assembly machine is an automated system that can assemble electronic components onto printed circuit boards (PCBs). This machine is designed to handle a wide range of components, including surface mount devices (SMDs), through-hole components, and mixed technology components. It is a crucial tool for electronics manufacturers as it helps to increase efficiency and accuracy while reducing production costs.
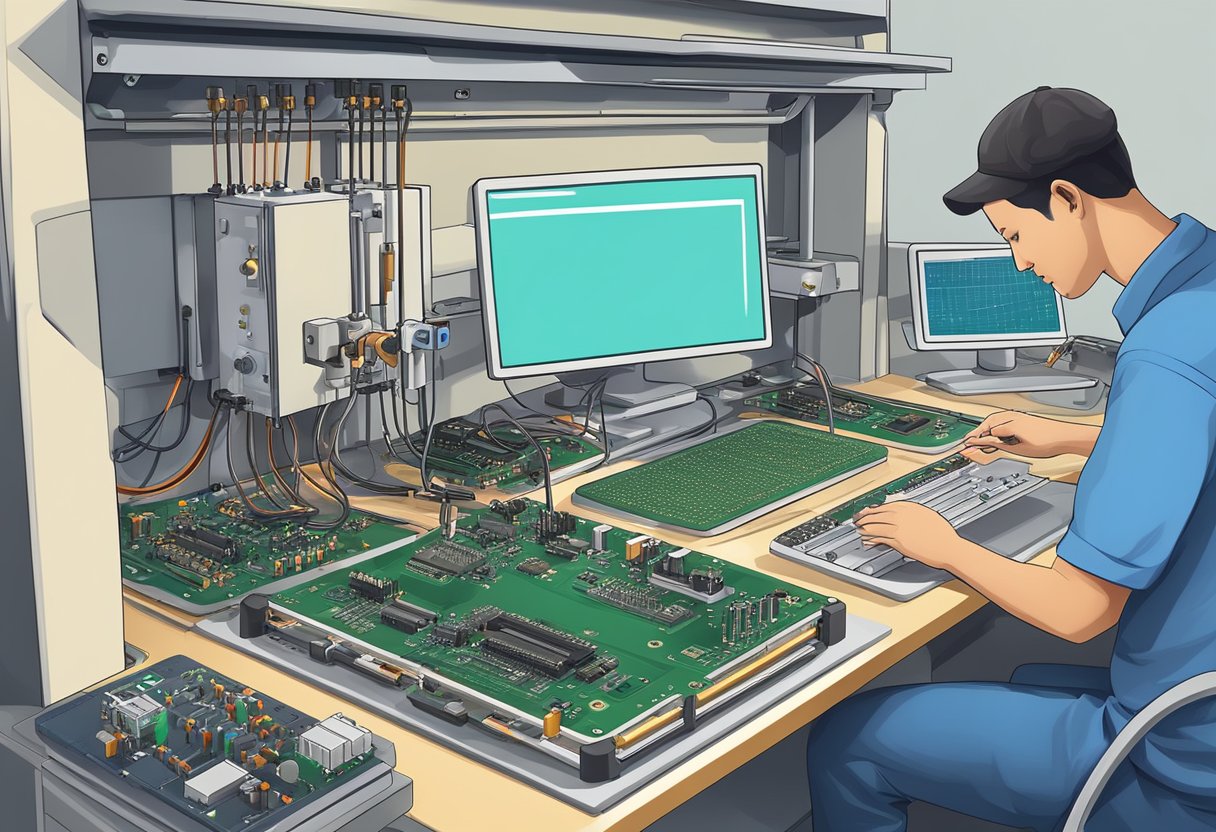
The assembly process involves placing components onto a PCB and then soldering them in place. The PCB components assembly machine can perform this process quickly and accurately, even for complex PCB designs. This is achieved through the use of advanced technologies such as computer vision, robotics, and artificial intelligence. These technologies enable the machine to identify and place components with high precision, ensuring that the finished product meets the required specifications.
Overview of PCB Assembly Machines
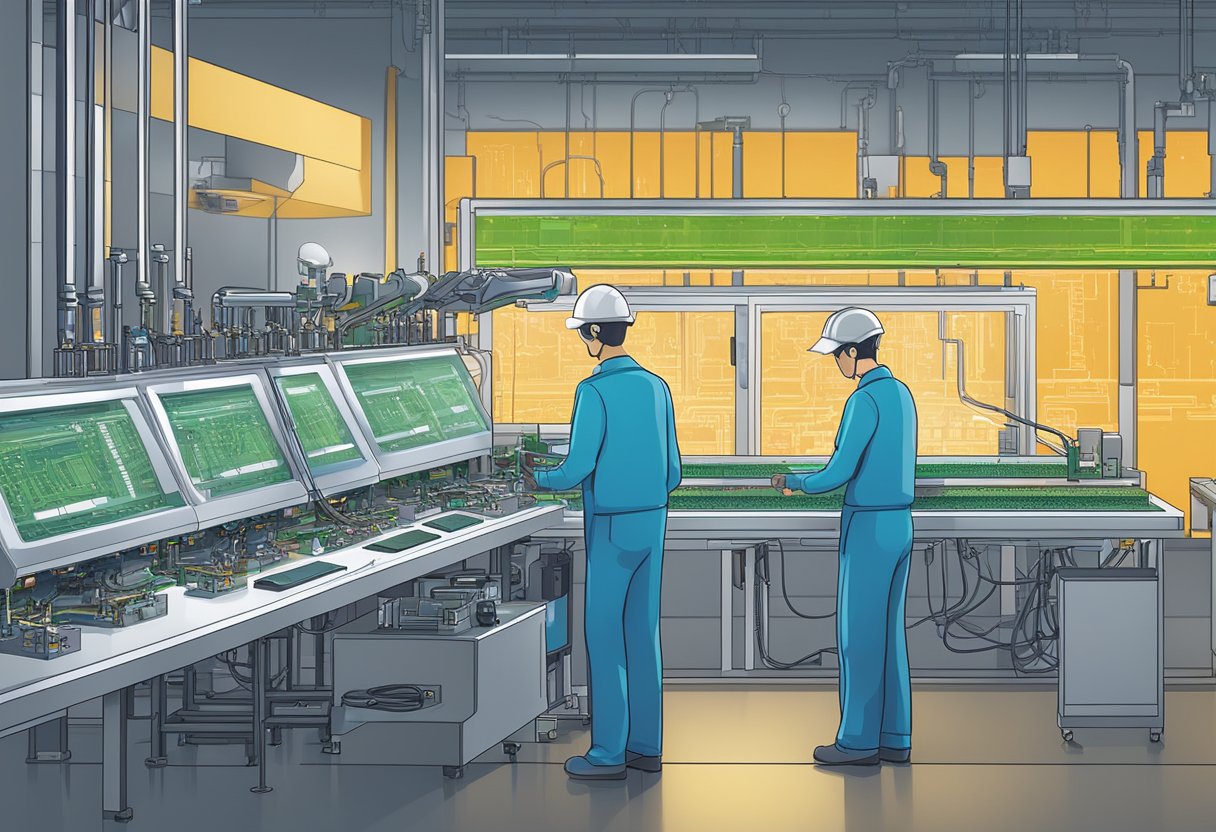
PCB assembly machines are automated machines that are used to assemble printed circuit boards (PCBs) with electronic components. These machines are designed to increase efficiency and accuracy in the assembly process. In this section, we will provide an overview of PCB assembly machines, including the types of assembly machines and their main functions.
Types of Assembly Machines
There are several types of PCB assembly machines available in the market. Each type of machine has its own unique features and capabilities. The most commonly used types of assembly machines are:
- Pick and Place Machines: These machines are used to pick up electronic components from a feeder and place them on the PCB. Pick and place machines can handle a wide range of component sizes and shapes, making them ideal for use in high-volume production environments.
- Reflow Ovens: These machines are used to heat the PCB and the components to a specific temperature, which causes the solder to melt and bond the components to the board. Reflow ovens are essential for surface-mount technology (SMT) assembly.
- Wave Soldering Machines: These machines are used to solder through-hole components to the PCB. The PCB is passed over a wave of molten solder, which wets the leads of the components and bonds them to the board.
Main Functions
The main functions of PCB assembly machines include:
- Component Placement: This function involves picking up components from a feeder and placing them on the PCB. Component placement is a critical step in the assembly process, as it determines the accuracy and quality of the final product.
- Soldering: This function involves bonding the components to the PCB using solder. Soldering can be done using either reflow ovens or wave soldering machines, depending on the type of components being used.
- Inspection: This function involves inspecting the PCB to ensure that all components are correctly placed and soldered. Inspection can be done manually or using automated inspection machines.
In conclusion, PCB assembly machines play a crucial role in the electronics manufacturing industry. They help to increase efficiency, accuracy, and quality in the assembly process. By understanding the different types of assembly machines and their main functions, manufacturers can choose the right machine for their specific needs.
Key Components of Assembly Machines
Assembly machines are complex systems that are designed to automate the process of assembling printed circuit boards (PCBs). These machines are made up of several key components that work together to ensure that the PCBs are assembled accurately and efficiently. In this section, we will discuss the three main components of assembly machines: placement heads, conveyor systems, and solder paste dispensers.
Placement Heads
Placement heads are one of the most important components of an assembly machine. These heads are responsible for picking up and placing the various components onto the PCB. There are several types of placement heads available, including vacuum, mechanical, and pneumatic. Vacuum placement heads are the most commonly used and are ideal for picking up small components such as resistors and capacitors. Mechanical placement heads are better suited for larger components such as connectors and ICs, while pneumatic placement heads are used for high-speed assembly.
Conveyor Systems
Conveyor systems are another important component of assembly machines. These systems are responsible for moving the PCBs through the assembly process. There are several types of conveyor systems available, including belt, chain, and roller conveyors. Belt conveyors are the most commonly used and are ideal for handling small to medium-sized PCBs. Chain conveyors are better suited for larger PCBs, while roller conveyors are used for high-speed assembly.
Solder Paste Dispensers
Solder paste dispensers are used to apply solder paste to the PCB before the components are placed. These dispensers are available in several types, including stencil printers, screen printers, and jet dispensers. Stencil printers are the most commonly used and are ideal for low to medium-volume production. Screen printers are better suited for high-volume production, while jet dispensers are used for high-speed assembly.
In conclusion, assembly machines are complex systems that are made up of several key components. Placement heads, conveyor systems, and solder paste dispensers are the three main components of assembly machines. Each component plays a crucial role in ensuring that the PCBs are assembled accurately and efficiently.
Software and Programming
Machine Control Software
The PCB components assembly machine is controlled by a sophisticated software system. This software allows the operator to program the machine to perform specific tasks, such as placing components on a circuit board or soldering connections. The software is user-friendly and can be customized to meet the specific needs of the user.
One of the key features of the machine control software is its ability to monitor the performance of the machine in real-time. This allows the operator to quickly identify any issues that may arise and take corrective action. The software also includes a variety of safety features to ensure that the machine operates safely and efficiently.
Optical Inspection Integration
In addition to the machine control software, the PCB components assembly machine also includes an optical inspection system. This system uses advanced imaging technology to inspect the components and connections on the circuit board. The inspection system is integrated with the machine control software, allowing the operator to quickly identify any defects or issues that may arise.
The optical inspection system is highly accurate and can detect even the smallest defects. This ensures that the finished circuit board meets the highest quality standards. The system is also highly efficient, allowing for rapid inspection of large quantities of circuit boards.
Overall, the software and programming of the PCB components assembly machine are critical to its performance and efficiency. The machine control software and optical inspection integration work together seamlessly to ensure that the machine operates safely, accurately, and efficiently.
Operational Efficiency
Efficiency is a crucial factor in the assembly of PCB components, as it affects the overall productivity of the assembly line. The use of a PCB components assembly machine can significantly improve operational efficiency in several ways.
Speed and Precision
One of the most significant advantages of using a PCB components assembly machine is the speed and precision that it offers. These machines can place components onto PCBs at a much faster rate than manual labor, which translates to a higher volume of production in a shorter time.
Moreover, the machine’s precision ensures that components are accurately placed in their designated locations, reducing the risk of errors and the need for rework. This precision also results in a higher quality of finished products, which can lead to increased customer satisfaction and loyalty.
Automation Levels
The level of automation in a PCB components assembly machine can also impact operational efficiency. Machines with higher levels of automation can perform tasks such as feeding components, placing them onto PCBs, and soldering them without human intervention.
This level of automation reduces the need for human labor, which can lead to cost savings and increased productivity. Additionally, machines with higher levels of automation can operate for longer periods without stopping, further increasing productivity.
In conclusion, the use of a PCB components assembly machine can significantly improve operational efficiency in terms of speed, precision, and automation levels. This efficiency can lead to increased productivity, cost savings, and higher quality finished products.