Ensuring Flawless Manufacturing: PCB Assembly Quality Control
As the technology-driven market grows, the demand for high-grade PCB assemblies has also escalated. These printed circuit boards are essential components that ensure the proper functioning of electronics, and any flaws or defects could lead to drastic consequences. Bearing this in mind, Winow New Energy Company, a leading name in the industry, devotes the utmost importance to stringent quality control throughout its assembly process. This article highlights Winow’s commitment to making sure that quality is kept up to standard all through assembling printed circuit boards. It further details the protocols, procedures, and advantages generated by their vigilant approach.
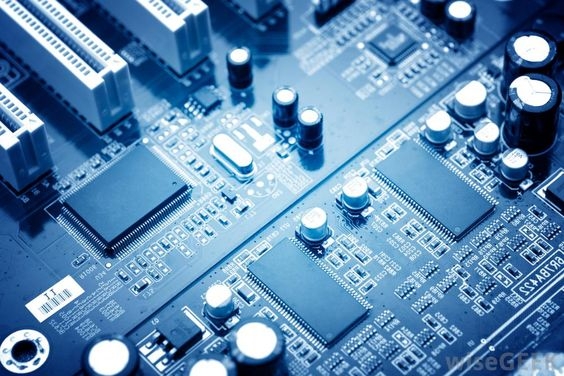
Requirements for Quality Control:
Winow New Energy Company recognizes that delivering reliable PCB assemblies requires a comprehensive quality control framework. To meet these requirements, the company focuses on the following key aspects:
1. Component Selection and Inspection:
Winow sources high-quality components from trusted suppliers and conducts thorough inspections to verify their authenticity and reliability. Rigorous quality checks, such as visual inspections, electrical testing, and component parameter verification, help identify any potential issues early in the assembly process.
2. Robust Manufacturing Processes:
Winow employs state-of-the-art equipment and advanced manufacturing processes to ensure precision and consistency during PCB assembly. Automated assembly lines minimize human error and enhance efficiency, while adherence to standardized operating procedures guarantees consistent quality across production batches.
Quality Control Procedures:
Winow New Energy Company employs a multi-step quality control process to maintain the highest standards throughout PCB assembly:
1. Incoming Material Inspection:
Upon receipt of components, Winow’s quality control team conducts comprehensive inspections to verify the quality, specifications, and compatibility of each component. This step eliminates the risk of using faulty or substandard materials in the assembly process.
2. Visual Inspection and Testing:
During assembly, Winow utilizes advanced imaging systems and automated optical inspection (AOI) machines to detect any visual defects, such as soldering issues, misalignment, or solder bridging. In addition, functional tests are conducted to ensure the proper functionality and performance of the assembled PCBs.
3. Statistical Process Control (SPC):
Winow leverages statistical process control techniques to monitor key parameters and maintain process stability. By analyzing data from various stages of the assembly process, the company can identify trends, deviations, and potential areas for improvement, leading to continuous refinement of its manufacturing processes.
Benefits of Quality Control:
Winow New Energy Company’s unwavering commitment to quality control in PCB assembly brings several notable benefits:
1. Enhanced Reliability:
By adhering to rigorous quality control measures, Winow ensures that its PCB assemblies meet or exceed industry standards. This results in highly reliable and durable electronic devices that perform consistently over their operational lifespan.
2. Customer Satisfaction:
Winow understands the importance of customer satisfaction and aims to deliver products that meet or exceed customer expectations. By maintaining strict quality control, they can provide defect-free PCB assemblies, resulting in improved customer satisfaction and loyalty.
3. Reduced Costs:
Effective quality control minimizes the occurrence of defects and the need for rework or repairs. This leads to reduced production costs, as resources are utilized efficiently, and wastage is minimized. Additionally, it helps prevent costly recalls or customer complaints due to substandard products.
Ensuring Excellence: How PCB Assembly Quality Control Drives Customer Satisfaction
I. The Significance of PCB Assembly Quality Control
Quality control is the foundation upon which successful PCB assembly processes are built. It involves a systematic approach to identify, prevent, and rectify defects or deviations in the assembly process. By implementing robust quality control procedures, manufacturers like Winow New Energy Company can ensure that each PCB assembly meets the highest standards of reliability, functionality, and durability. This commitment to quality control is pivotal for achieving customer satisfaction.
II. Implementing Rigorous Inspection Protocols
To maintain excellence in PCB assembly, Winow New Energy Company employs rigorous inspection protocols at various stages of the manufacturing process. The initial step involves meticulous inspection of incoming components to verify their authenticity, quality, and compatibility. Throughout the assembly process, inspections are carried out to identify and rectify any potential issues promptly. Visual inspection, automated optical inspection (AOI), and X-ray inspection are some of the techniques used to detect defects, such as soldering anomalies, component misalignment, or insufficient solder paste.
III. Utilizing Advanced Testing Procedures
Beyond inspections, comprehensive testing procedures play a crucial role in ensuring the quality of PCB assemblies. Winow New Energy Company incorporates advanced testing methodologies to verify the functionality, performance, and reliability of its products. Functional testing ensures that the assembled PCBs meet the intended operational requirements. Environmental and reliability testing, such as temperature cycling and vibration testing, simulates real-world conditions to assess the PCB’s durability and longevity. Thorough testing guarantees that only reliable and high-quality PCB assemblies are delivered to customers.
IV. Adhering to Industry Standards and Certifications
To further reinforce its commitment to quality control, Winow New Energy Company strictly adheres to industry standards and certifications. Compliance with international standards, such as ISO 9001:2015 and IPC-A-610, ensures that their PCB assemblies meet globally recognized quality benchmarks. Certifications validate the manufacturer’s capability to consistently produce reliable products, instilling confidence in customers and fostering long-term relationships.
V. Continuous Improvement and Feedback Integration
Winow New Energy Company understands that quality control is an ongoing process. They actively seek feedback from customers, conduct regular internal audits, and analyze quality data to identify areas for improvement. This commitment to continuous improvement enables them to refine their processes, address any potential issues proactively, and optimize the overall quality of their PCB assemblies. By listening to customer feedback, they can exceed expectations and build lasting partnerships based on trust and satisfaction.
Conclusion:
Winow New Energy Company goes to great measures in ensuring that its PCB assembly is of the highest quality. From careful component selection to aggressive quality controls, Winow is vigilant in delivering the most reliable capabilities for its electronics products. By placing emphasis on quality, Winow establishes itself as a trustworthy manufacturer for customers looking to purchase top-notch electronic components. From the quest to meet the demands of today’s technology to powering devices and equipment that will shape tomorrow’s future, Winow New Energy Company is proud to uphold its benchmark in utilizing stringent quality control procedures for its PCB assemblies.