How to Make a Flexible PCB for Your Next Project
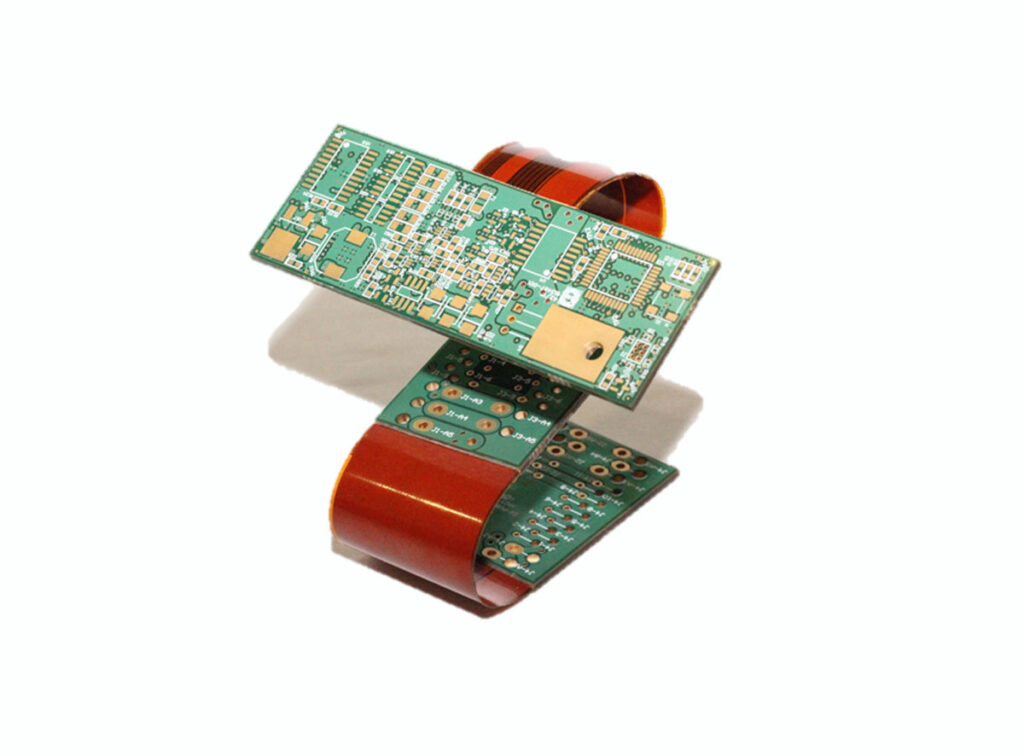
There are several ways to make a PCB flexible:
- Using a flexible substrate: Instead of using traditional rigid materials, such as fiberglass or epoxy, a flexible substrate material, such as polyimide or polyester, is used as the base material for the PCB. These materials can bend and flex without breaking.
- Using a flexible circuit board: Instead of traditional PCBs, a flexible circuit board can be used. Flexible circuit boards are made by laminating a thin layer of metal, such as copper, onto a flexible substrate material. This allows the circuit to bend and flex with the substrate.
- Using a combination of rigid and flexible PCBs: Some designs may use a combination of rigid and flexible PCBs, which can be interconnected using a flexible cable or connector. This approach allows for flexibility in certain areas of the circuit while maintaining the structural integrity of the circuit in other areas.
- Using flexible PCBs with bendable components: To make a PCB more flexible, some components can be replaced with bendable components. This makes the PCB more versatile and can be used in applications where traditional PCBs would be too stiff or brittle.
It is important to note that, while flexible PCBs can be bent and flexed, they still have limitations on how much they can be bent and flexed, and the number of times they can be flexed before they become damaged.
How Do You Make A PCB Flexible?
PCBs are an essential part of any electrical or electronic device. They are used for a variety of applications including computers, mobile devices, and other appliances. So how do you make a PCB flexible?
A PCB is made up of two main parts: a base material and copper traces. They’re made of special materials that can withstand being bent, so they’re often used in products such as mobile phones and wearable devices where flexibility is important.
The base material is usually fiberglass or epoxy resin, while the copper traces are made of thin sheets of metal attached to the base material using soldering techniques. When electricity passes through these traces, it is able to travel through the entire circuit board without being interrupted by anything else on its way there.
Build A Flexible PCB – Tips And Tricks
Flexible PCB Manufacturing design is a complex process that requires a lot of skill and experience. The first step in designing a Flexible PCB is creating the schematic. The schematic is the blueprint for your circuit and shows how it will be built. The next step is to create the layout, which involves placing all components on the board and connecting them together with traces.
When designing a Flexible PCB, you need to consider many factors such as component placement, trace spacing, ground planes, power planes, via density, and more. For example, when placing components on a board there are many ways to optimize your design but you need to decide what’s best for your specific application.
So how do you make a PCB flexible? The following tips will help you get started on building your own flexible PCB:
- 1) Consider whether or not it needs to be flexible
- 2) Choose your materials carefully
- 3) Use vias instead of jumpers
- 4) Keep track of how much current flows through each trace
Things You Should Know When Making A Flexible PCB
Flexible PCBs are not just used for making bendable devices but also for other purposes like making wearable electronics and conducting other electronic devices that need to be worn on the body.
The following are some of the things you should know when making a flexible PCB:
1. The Flexibility of Flexible PCBs
Flexible PCBs have a very high degree of flexibility which makes them suitable for use in many different devices and applications. They can be bent without causing any damage to them or affecting their performance.
So how do you make a PCB flexible? The flexibility of flexible PCBs has been made possible by the use of materials such as FR4, which is used to make rigid boards, but it has been modified to increase its toughness and its ability to withstand bending. The process involves adding a layer of glass-filled epoxy resin between two layers of FR4 laminate.
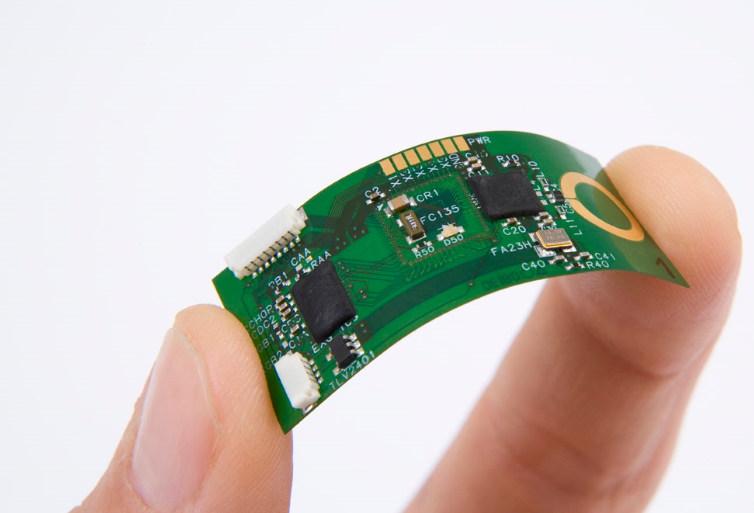
2. The Manufacturing Processes Used For Flexible Circuit Boards
The manufacturing process used for these circuits differs from the traditional ones used for making rigid circuit boards because you need an extra layer of insulation around the components that make up your circuit board which allows them to bend without breaking or damaging any part of your board.
3. Flexible Boards Can Be Used In Many Different Applications
Flexible boards can be used in many different applications including:
- Medical devices – such as heart monitors and pacemakers.
- Wearable technology – such as smartwatches and fitness trackers.
- Electronics such as smartphones and tablets.
Easy Steps To Flexing Your PCB
Step 1: Select your flex PCB supplier
If you’re just getting into flex PCB manufacturing, the first step is to find a supplier such as WINOW. There are many companies that offer flexible printed circuit boards for commercial and industrial applications. They will have different capabilities and limitations, so it’s important to know what you need before deciding on a specific vendor.
Step 2: Decide on design requirements
Next, it’s time to consider your design requirements. Will the board be used in an environment where it will be exposed to extreme temperatures? How thick do you want the board to be? What kind of materials will be used in production? All of these factors will affect how you design your board in order to meet these requirements.
Step 3: Design your flex PCB
Once you have chosen a supplier and have decided on your design requirements, it’s time to start designing your own flex PCB! So how do you make a PCB flexible? This process can range from relatively simple designs that only need one layer of copper traces with no special features all the way up to complex designs with multiple layers of copper traces, vias (interconnects), and other features like solder masks or silk screening.
Why Do Some Electronics Have Flexible PCBs?
Flexible circuit boards are designed for applications where you need to be able to bend or flex the board itself. They’re made out of flexible materials like polymer rather than rigid materials like ceramics or glass used in traditional PCBs. Flexible circuits can be found in everything from wearable devices to medical equipment and even solar panels.
The main reason for using Flexible PCBs is to save space. These boards are used in the medical industry, where there is a need for compact and flexible electronics. For example, if you want to make a small portable device that can be worn on your wrists, such as a smartwatch or a fitness tracker, then you will need to use a flexible board.
The other reason why we use Flexible PCBs is that they are more durable than rigid boards. This makes them ideal for use in applications where there is a risk of damage from impacts or drops. For example, if you want to make an electronic device that can withstand water damage or high temperatures, then you should use a flexible board instead of an ordinary rigid one.
Conclusion
Now, do you understand how do you make a PCB flexible? With rich experience in Flexible PCB Manufacturing, WINOW can provide customized service to meet all your needs. Please check the WINOW website to find your answer.