Flexible Circuit Board vs. Traditional PCB: Which One Should You Choose?
As technology continues to evolve, electronics manufacturers are coming up with new ways to improve the efficiency of their devices. One popular innovation has been the flexible circuit board (FCB). These two options offer unique advantages and applications, making the choice between them a crucial decision in electronics design and manufacturing.
The Rise of Flexible Circuit Board
Flexible circuit board, also known as flex PCBs or FPC, is a remarkable evolution in electronic engineering. These boards are designed to bend and twist without sacrificing functionality. They are constructed from flexible and lightweight materials, such as polyimide or polyester, which make them ideal for applications where traditional rigid PCBs simply won’t cut it.
Imagine a smartwatch that wraps comfortably around your wrist or a foldable smartphone that can be compact when needed and expanded for a larger screen. Flexible circuit boards have made these futuristic designs a reality. Winow New Energy Co., LTD (Dongguan), a prominent flexible circuit board manufacturer, is at the forefront of this revolution.
Flex vs. Rigid: When to Choose Flexible Circuit Board for Your Project
To understand the decision between flexible circuit boards and traditional PCBs, it’s important to grasp the fundamental differences between the two. Traditional PCBs are typically rigid and inflexible, composed of layered substrates with conductive traces etched onto them. In contrast, flexible circuit boards, as the name suggests, are designed to be pliable. They are constructed using flexible substrate materials, allowing for a variety of shapes, sizes, and bending capabilities.
Flexible circuit boards have several advantages over their rigid counterparts. Their flexibility and adaptability make them ideal for applications where space is limited, or where the board needs to conform to a non-standard shape or contour. This is especially useful in industries like aerospace, automotive, medical devices, and wearable technology, where space constraints and the need for durability and reliability are paramount.
Another key advantage of flexible circuit boards is their weight savings. Traditional PCBs are bulkier and heavier, which can be a significant drawback in applications where weight is a critical factor. Flexible circuit boards are lightweight and can be designed to meet specific weight requirements, making them an excellent choice for industries like aerospace and automotive, where reducing weight can improve fuel efficiency and performance.
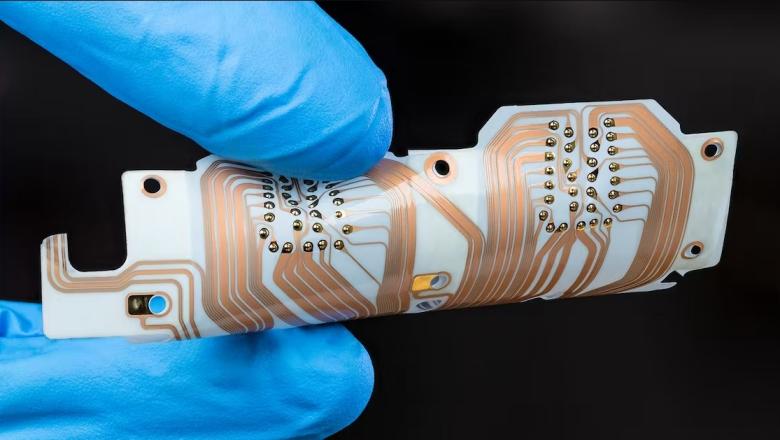
When to Choose a Flexible Circuit Board for Your Project
1. Space Constraints: When space is limited, and a compact design is a must, flexible circuit boards shine. They can be bent or folded to fit snugly into tight spaces, making them ideal for applications in the medical, automotive, and aerospace industries.
2. Complex and Multilayered Designs: Flexible circuit boards are a great choice when your project requires intricate, multilayered designs. Their flexibility accommodates the integration of numerous components and connections in a compact space.
3. High-Temperature Environments: In applications where high temperatures are a concern, flexible circuit boards made with materials like polyimide are known for their excellent thermal stability and performance.
4. Vibration and Shock Resistance: If your project involves environments with constant vibrations or mechanical stress, flexible circuit boards can handle it better than rigid PCBs. They’re more resistant to damage and less prone to cracking or breaking.
The Pros and Cons of Flexible Circuit Boards in Your Electronic Project
Pros of Using Flexible Circuit Boards
1. Space Efficiency: One of the most significant advantages of using flexible circuit boards is their space-saving design. Traditional rigid PCBs cannot be bent, which can limit their use in compact electronics. Flex PCBs, on the other hand, can be designed to fit snugly into tight spaces, maximizing the use of available room.
2. Weight Reduction: The lightweight nature of flexible circuit boards makes them perfect for applications where weight is a critical factor, such as the electric and automotive industries. This not only saves space but also reduces fuel consumption and production costs.
3. Reliability: Flex PCBs often have fewer solder joints and connectors, reducing the risk of potential failure points. This makes them highly reliable, which is crucial in applications where downtime is not an option.
4. Durability: Their flexibility doesn’t compromise their durability. Flex PCBs can withstand bending, twisting, and other physical stresses, making them perfect for applications that involve movement or vibrations.
Cons of Using Flexible Circuit Boards
1. Cost: Flexible circuit boards can be more expensive to manufacture compared to their rigid counterparts. The materials and processes involved in producing flex PCBs can drive up the cost of production.
2. Complex Design: Designing flexible circuit boards can be more complex. The flexibility of these boards requires precise design and attention to detail. This can be a challenge for some engineers.
3. Limited Layer Count: Flex PCBs typically have a limited number of layers compared to rigid boards, which can be a drawback for complex electronic systems that require many interconnected components.
Bending the Rules of Electronics: A Deep Dive into Flexible Circuit Board Design
The design and fabrication of flexible circuit board are a fascinating blend of art and science. The process involves using flexible substrates, such as polyimide, PET (polyethylene terephthalate), or PEEK (polyether ether ketone). These materials can be bent, twisted, and folded, allowing engineers to create boards that conform to intricate shapes and spaces.
One manufacturer that has excelled in producing high-quality flexible circuit boards is Winow New Energy Co., LTD, based in Dongguan, China. With their expertise in flexible PCB design and manufacturing, they have contributed significantly to various industries by offering cutting-edge solutions.
The flexibility of these boards is achieved through carefully designing conductive traces and vias, allowing them to withstand repeated bending and flexing without compromising the electrical connections. Additionally, components like connectors, integrated circuits, and passive components must also be chosen and placed strategically to ensure they can endure the rigors of bending and flexing.
Furthermore, flexible circuit boards can be single-sided, double-sided, or multilayered, offering a range of options for different project requirements. Multilayer designs, for instance, are used in complex applications where additional functionality and connections are necessary.
Conclusion
The choice between flexible circuit board and traditional PCBs depends on the specific needs of your project. Flexible circuit board is the ideal solution for applications requiring lightweight, compact, and adaptable designs, such as in the automotive, and medical industries. Thanks to their pliability and the expertise of manufacturers like Winow New Energy Co., LTD, these boards are pushing the boundaries of what’s possible in the world of electronics.