Flexibility and reliability with a proven flex PCB manufacturer
When it comes to electronic device production, flexibility, and reliability are paramount. This is where a reliable flex PCB manufacturer comes into play. A flex PCB (Flexible Printed Circuit Board) offers numerous advantages, such as space-saving, exceptional bending capabilities, and improved signal integrity. In this blog, we will explore the importance of a proven flex PCB manufacturer and delve into the processes and insights provided by Winow New Energy Co., Ltd (Dongguan), a leading flex PCB manufacturer, to achieve flexibility and reliability in electronic designs.
Unveiling the Processes of a Trusted Flex PCB Manufacturer
A trusted flex PCB manufacturer like Winow New Energy Co., Ltd (Dongguan) follows a meticulous manufacturing process to ensure the highest quality and performance. Here are the key processes involved in flex PCB manufacturing:
1. Design and Layout
The design and layout phase is crucial to determine the flexibility and reliability of the flex PCB. A skilled team of engineers works closely with clients to understand their requirements and design a layout that meets their needs. Design considerations include component placement, signal integrity, and adequate spacing to accommodate bending or flexing.
2. Material Selection
Choosing the right materials is crucial for the performance and longevity of a flex PCB. A trusted manufacturer like Winow New Energy Co., Ltd (Dongguan) provides guidance on material selection based on the specific needs of the project. Factors such as thermal conductivity, dielectric constant, flexibility, and durability are taken into account to ensure optimal performance.
3. Manufacturing and Assembly
The manufacturing and assembly stage involves the fabrication of the flex PCB and the assembly of electronic components. State-of-the-art equipment and advanced techniques are utilized to ensure precision and reliability. Surface mount technology (SMT) is commonly used for component placement and soldering, resulting in compact and reliable assembly.
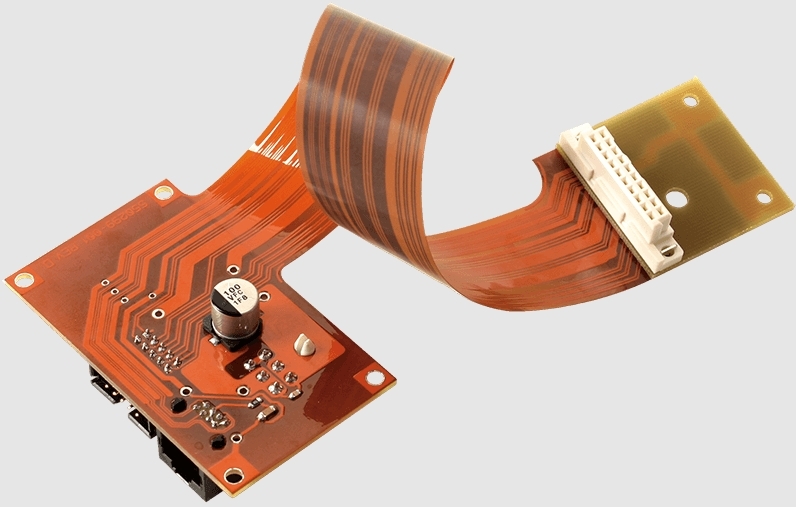
Flex PCB Manufacturer Insights: Optimizing Design and Efficiency
Working with a proven flex PCB manufacturer like Winow New Energy Co., Ltd (Dongguan) offers valuable insights to optimize design and improve efficiency. Here are some key insights provided by leading flex PCB manufacturers:
1. Collaborative Design Approach
A trusted manufacturer understands the importance of a collaborative design approach. They work closely with clients to understand their design requirements, functional specifications, and constraints. This collaboration ensures that the flex PCB design meets the desired performance and flexibility goals.
2. Design-for-Manufacturability (DFM) Analysis
A critical aspect of efficient flex PCB manufacturing is conducting a Design-for-Manufacturability (DFM) analysis. This analysis involves identifying potential design issues early in the process to reduce the need for future modifications and improve efficiency. A proven it will utilize their expertise to provide DFM feedback to clients, resulting in a more optimized design.
3. Prototyping Services
Prototyping plays a crucial role in the development cycle of any electronic design. A trusted flex PCB manufacturer offers prototyping services to allow clients to test and refine their designs before moving into full-scale production. This iterative process ensures that the final product meets the desired specifications and performs reliably.
How to Evaluate a Flex PCB Manufacturer: Key Factors to Consider
Selecting the right flex PCB manufacturer is essential for achieving flexibility and reliability in electronic designs. Here are some key factors to consider when evaluating a flex PCB manufacturer:
1. Experience and Reputation
Consider the experience and reputation of the flex PCB manufacturer in the industry. Look for manufacturers with a proven track record of delivering high-quality products and meeting customer expectations.
2. Manufacturing Capabilities
Assess the manufacturer’s manufacturing capabilities, including their equipment, processes, and certifications. A well-equipped manufacturer with advanced technology and certifications ensures that they can handle the complexities of flex PCB manufacturing.
3. Quality Control and Testing
Evaluate the manufacturer’s quality control and testing processes. Ensure that they have stringent quality control measures in place to identify and rectify any potential issues during the manufacturing process. An emphasis on reliability and thorough testing guarantees a high-quality end product.
Flex PCB Manufacturer Excellence: Delivering High-Quality Solutions
A trusted flex PCB manufacturer like Winow New Energy Co., Ltd (Dongguan) excels in delivering high-quality solutions that meet the specific needs of clients. Through their expertise and commitment to excellence, they ensure that flex PCBs are manufactured to the highest standards. Here are some key factors that contribute to their success:
1. Design Optimization
A proven flex PCB manufacturer understands the importance of design optimization. They work closely with clients to understand their requirements and provide valuable insights to improve the design. This collaborative approach helps to achieve optimal performance, reliability, and flexibility in the final product.
2. Material Selection
The choice of materials is critical in flex PCB manufacturing. Winow New Energy Co., Ltd (Dongguan) offers guidance on material selection based on the specific needs of the project. They consider factors such as thermal conductivity, dielectric constant, flexibility, and durability to ensure that the selected materials contribute to the overall performance and reliability of the flex PCB.
3. Advanced Manufacturing Techniques
Winow New Energy Co., Ltd (Dongguan) utilizes advanced manufacturing techniques to ensure precision and quality. State-of-the-art equipment and processes allow for accurate fabrication and assembly of flex PCBs. Surface mount technology (SMT) is commonly employed for component placement and soldering, resulting in compact and reliable assemblies.
Exploring Flex PCB Manufacturing Techniques with a Leading Manufacturer
Flex PCB manufacturing involves a range of techniques and processes to ensure the highest quality and performance. Partnering with a leading manufacturer like Winow New Energy Co., Ltd (Dongguan) provides valuable insights into these techniques. Here are some key manufacturing techniques employed by renowned flex PCB manufacturers:
1. Surface Treatment
Surface treatment is an important step in flex PCB manufacturing. This process involves cleaning and preparing the surface of the PCB to enhance adhesion properties and prevent oxidation. Surface treatment techniques such as immersion gold, OSP (Organic Solderability Preservatives), and ENIG (Electroless Nickel Immersion Gold) are commonly used to improve solderability and protect the flex PCB.
2. Laser Cutting and Drilling
Laser cutting and drilling are advanced techniques employed in the manufacturing of flex PCBs. It laser technology enables precise and intricate cuts and drills, contributing to the flexibility and reliability of the PCB. Laser cutting and drilling also allow for the creation of complex designs and patterns, enabling the PCB to fit into tight spaces without compromising its performance.
3. Testing and Quality Control
Thorough testing and quality control measures are essential in flex PCB manufacturing. Renowned manufacturers conduct extensive testing to ensure that the flex PCBs meet the required specifications and performance standards. This includes electrical testing, impedance control, solderability testing, and visual inspections. Rigorous quality control measures help to identify and rectify any potential issues, resulting in reliable and high-quality flex PCBs.
Flex PCB Manufacturer Best Practices: Ensuring Design Success
To ensure the success of your flex PCB design, it is important to follow best practices recommended by reputable manufacturers. Here are some key best practices to consider:
1. Collaborative Design Approach
Engage in a collaborative design process with your it. Clearly communicate your requirements and actively seek their insights and expertise. This collaborative approach will result in a well-optimized design that meets your expectations in terms of functionality, flexibility, and reliability.
2. Thorough Design Review
Perform a thorough design review with your manufacturer to identify any potential design issues early on. This comprehensive review allows for necessary modifications and refinements to be made, ensuring that your design is optimized for successful production.
3. Regular Communication
Maintain regular communication with your flex PCB manufacturer throughout the production process. This open line of communication allows for timely feedback and updates, ensuring that any changes or adjustments can be addressed promptly. Regular communication fosters a strong working relationship and helps to ensure the success of your project.
Conclusion
Flexibility and reliability are crucial in electronic designs, and a trusted flex PCB manufacturer is key to achieving these goals. Winow New Energy Co., Ltd (Dongguan) exemplifies the qualities of a proven flex PCB manufacturer, offering meticulous processes, valuable insights, and a commitment to quality. By partnering with a reliable flex PCB manufacturer like Winow New Energy Co., Ltd (Dongguan), businesses can ensure that their electronic designs are flexible, reliable, and optimized for success.