Unlock the Potential of Flex PCB Assembly!
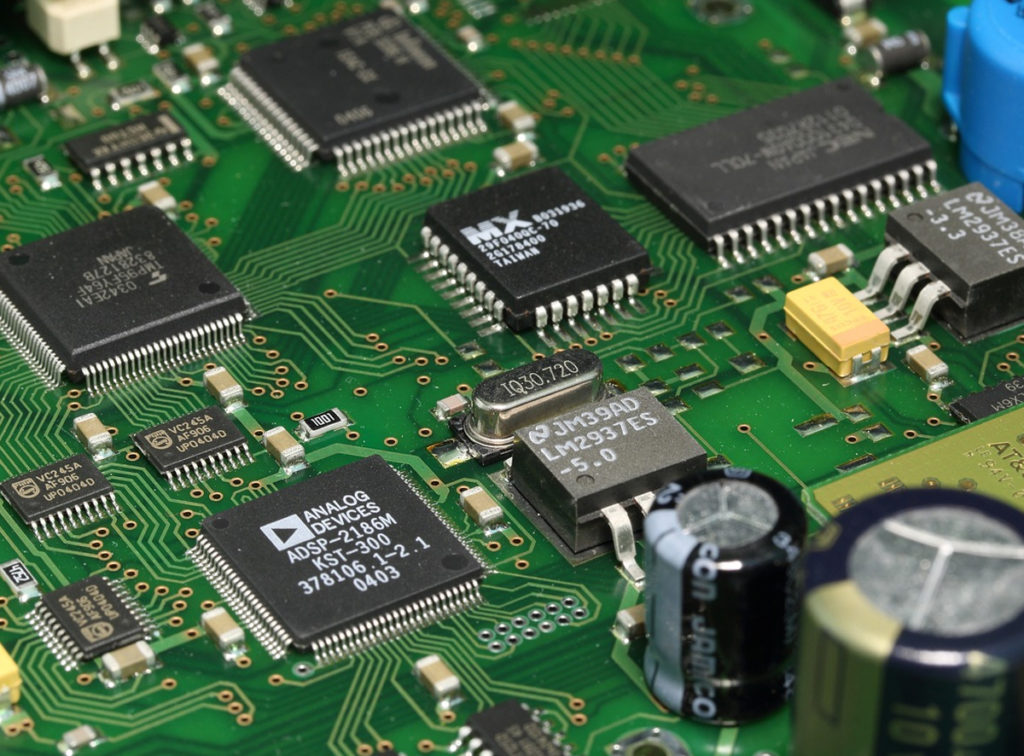
Flex PCB assembly is a great way to build custom circuits and systems for various applications. It is a cost-effective solution that can reduce development costs and improve the reliability of products. Flex PCB assembly offers a variety of advantages, such as flexibility, scalability, and the ability to integrate components into complex designs. In this blog, we’ll explore the basics of flex PCB assembly, its benefits, process, components, standards, materials, design tips, testing, and services. So let’s get started!
What is Flex PCB Assembly?
Flex PCB assembly is an advanced technology that enables designers and engineers to create flexible, lightweight, and space-saving printed circuit boards (PCBs). It utilizes thin and flexible materials to construct PCBs with multiple layers of copper traces and components that can be bent or folded. Flex PCB assembly offers a variety of benefits, including the ability to reduce the size and weight of products, increase mechanical stability, and improve system performance.
The process of flex PCB assembly begins with the design of the PCB. This involves laying out the copper traces and components on a thin, flexible substrate, such as polyimide or polyester. The next step is to solder the components onto the board, followed by the application of protective layers to the board. Once the board is complete, it is tested and inspected to ensure it meets the intended design and performance requirements.
Benefits of Flex PCB Assembly
Flex PCB assembly offers a variety of advantages that make it an attractive option for a wide range of applications.
The first benefit is the ability to create complex designs with fewer components. Flex PCBs can be bent into various shapes, allowing designers and engineers to build intricate circuits and systems with fewer components. This reduces the cost of development and improves product reliability.
Flex PCBs also offer better mechanical stability. They are less prone to vibration, shock, and temperature changes, making them ideal for applications that require high levels of reliability. Additionally, flex PCBs are lightweight and can be flexed or folded into tight spaces, which makes them ideal for applications where space is limited.
Finally, flex PCBs are highly scalable. They can be used to create a wide range of products, from simple circuits to highly complex systems. This makes them ideal for a variety of applications, from automotive to consumer electronics.
Flex PCB Assembly Process
The process of flex PCB assembly begins with the design of the board. This involves laying out the copper traces and components on a thin flexible substrate, such as polyimide or polyester. The next step is to solder the components onto the board, followed by the application of protective layers to the board. Once the board is complete, it is tested and inspected to ensure it meets the intended design and performance requirements.
The next step in the process is to apply the soldering paste. This is done using a solder mask, which is a stencil-like material that helps to control the flow of the solder paste. The paste is then applied to the board using a stencil printer or dispenser. Once the paste has been applied, it needs to be reflowed, which involves heating the board to a specific temperature to activate the solder.
After reflow, the board is inspected to ensure that there are no shorts or opens in the solder joints. Once the board has passed inspection, it is ready for the application of the protective layers. These layers are typically applied using a lamination process, which involves bonding the layers together with a special adhesive.
Flex PCB Assembly Components
Flex PCB assembly requires a number of components, ranging from printed circuit boards to components that are soldered onto the board. The most common components used in flex PCB assembly are:
- Flexible substrates: These are thin, flexible materials such as polyimide or polyester that form the base of the flex PCB.
- Solder paste: This is a paste-like material that is used to attach components to the board.
- Solder mask: This is a stencil-like material that helps to control the flow of the solder paste.
- Solder reflow ovens: These are used to heat the board to a specific temperature to activate the solder.
- Laminating equipment: This is used to bond the protective layers to the board.
- Testing equipment: This is used to inspect the board and ensure that it meets the intended design and performance requirements.
Flex PCB Assembly Standards
Flex PCB assembly is governed by a number of standards that ensure the reliability of the board. These standards include IPC-2221, IPC-2223, and IPC-2224. These standards define the design, fabrication, and assembly requirements of flex PCBs.
IPC-2221 is the most commonly used flex PCB assembly standard. It covers the design, fabrication, and assembly of flexible printed boards. It includes requirements for minimum trace width, minimum trace spacing, and minimum solder mask thickness.
IPC-2223 is another flex PCB assembly standard that covers the fabrication and assembly of flexible printed boards. It includes requirements for minimum trace width, minimum trace spacing, and minimum solder mask thickness.
IPC-2224 is the most recent flex PCB assembly standard. It covers the design, fabrication, and assembly of flexible printed boards. It includes requirements for minimum trace width, minimum trace spacing, and minimum solder mask thickness.
Flex PCB Assembly Materials
Flex PCB assembly requires a variety of materials, ranging from flexible substrates to solder pastes. The most commonly used materials in flex PCB assembly are:
- Flexible substrates: These are thin, flexible materials such as polyimide or polyester that form the base of the flex PCB.
- Solder paste: This is a paste-like material that is used to attach components to the board. It typically contains flux, tin, and solder alloy.
- Solder mask: This is a stencil-like material that helps to control the flow of the solder paste. It typically contains an adhesive that helps to keep the solder paste in place.
- Copper foil: This is the material used to create the copper traces on the flex PCB. It usually consists of copper-coated paper or plastic.
- Lead-free solder: This is a type of solder that does not contain lead and is used to attach components to the board.
- Adhesive: This is used to bond the protective layers to the board. It typically contains an epoxy-based material.
Flex PCB Assembly Design Tips
Flex PCBs are highly complex and require a great deal of design expertise. Here are some design tips to help ensure the reliability of your flex PCBs:
- Pay close attention to the trace width and spacing requirements. The trace width and spacing requirements specified in the IPC-2221, IPC-2223, and IPC-2224 standards must be followed closely to ensure the reliability of the board.
- Use high-quality materials. It is important to use high-quality materials when designing flex PCBs. This includes using high-quality flexible substrates and solder pastes.
- Use the correct soldering technique. The soldering technique used should be appropriate for the type of components being soldered.
- Ensure proper reflow. The reflow process should be performed correctly to ensure that the solder joints are strong and reliable.
- Use the right testing equipment. The testing equipment used should be appropriate for the type of board being tested.
Flex PCB Assembly Testing
Flex PCBs must be tested to ensure that they meet the intended design and performance requirements. The testing process typically involves visual inspection, electrical testing, and environmental testing.
Visual inspection is used to check for any defects in the board. This includes checking for shorts, opens, and incorrect polarities. Electrical testing is used to check the electrical characteristics of the board, such as resistance, capacitance, and inductance. Environmental testing is used to check the board’s ability to withstand temperature, vibration, and shock.
Flex PCB Assembly Services
Flex PCB assembly services are available from a variety of companies. These services typically include the design and fabrication of flex PCBs, as well as the assembly of components onto the boards.
These services can help to reduce the cost and time associated with flex PCB assembly. They also provide access to experts who can help to ensure that the board meets the intended design and performance requirements.
Conclusion
Flex PCB assembly is an advanced technology that offers a variety of benefits, such as flexibility, scalability, and the ability to integrate components into complex designs. It requires a variety of components, materials, and standards to ensure the reliability of the board. Additionally, flex PCBs must be tested to ensure that they meet the intended design and performance requirements.
Flex PCB assembly services are available from a variety of companies and can help to reduce the cost and time associated with flex PCB assembly. So, if you’re looking to unlock the potential of flex PCB assembly, consider taking advantage of these services.