Fast Turn PCB Assembly: Quick and Efficient Solutions for Your Electronics
Fast turn PCB assembly is a process that allows for quick and efficient production of printed circuit boards. This type of assembly is particularly useful for companies that need to produce small or medium-sized batches of PCBs quickly. Fast turn PCB assembly can help businesses save time and money, as well as improve their overall productivity.
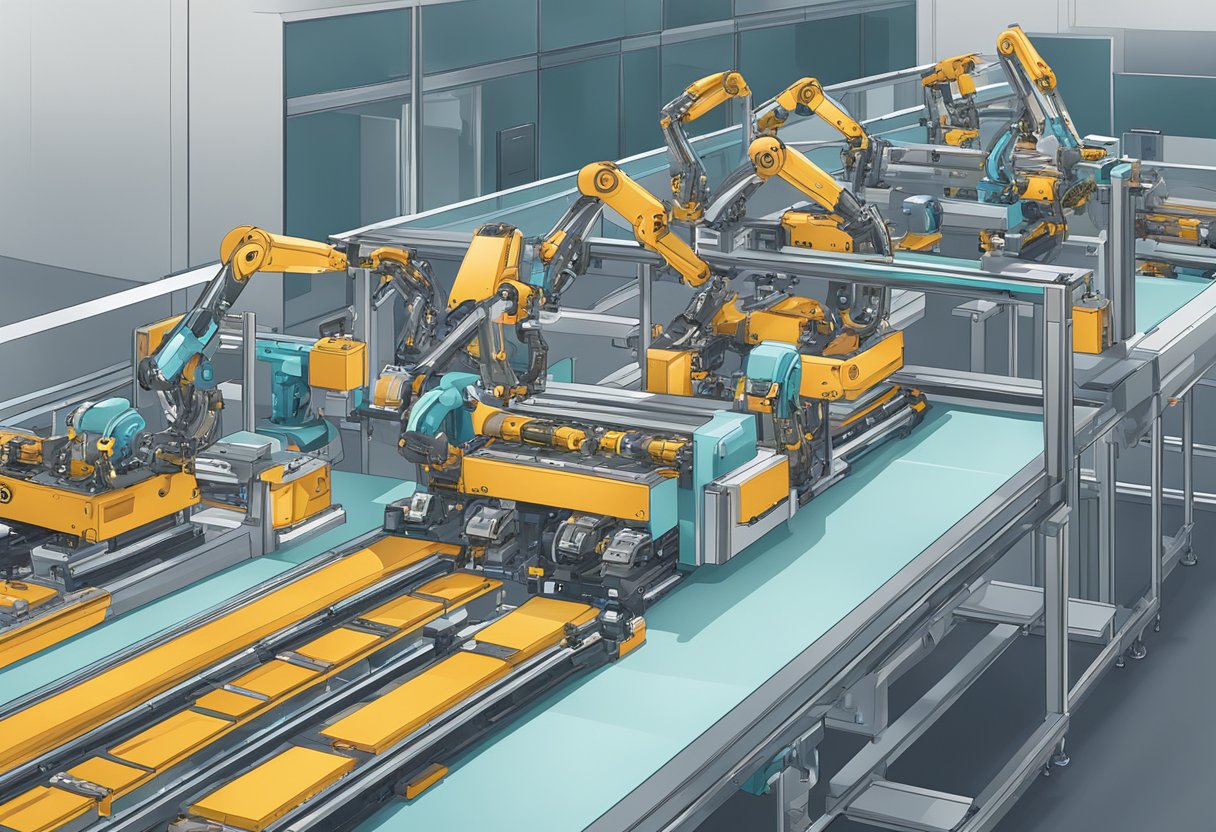
The process of fast turn PCB assembly involves using advanced technology and specialized equipment to quickly and accurately produce printed circuit boards. This process can be completed in a matter of hours or days, depending on the complexity of the design and the size of the batch. Fast turn PCB assembly is ideal for companies that need to produce prototypes quickly or for those that need to make changes to their designs on the fly.
Overview of Fast Turn PCB Assembly
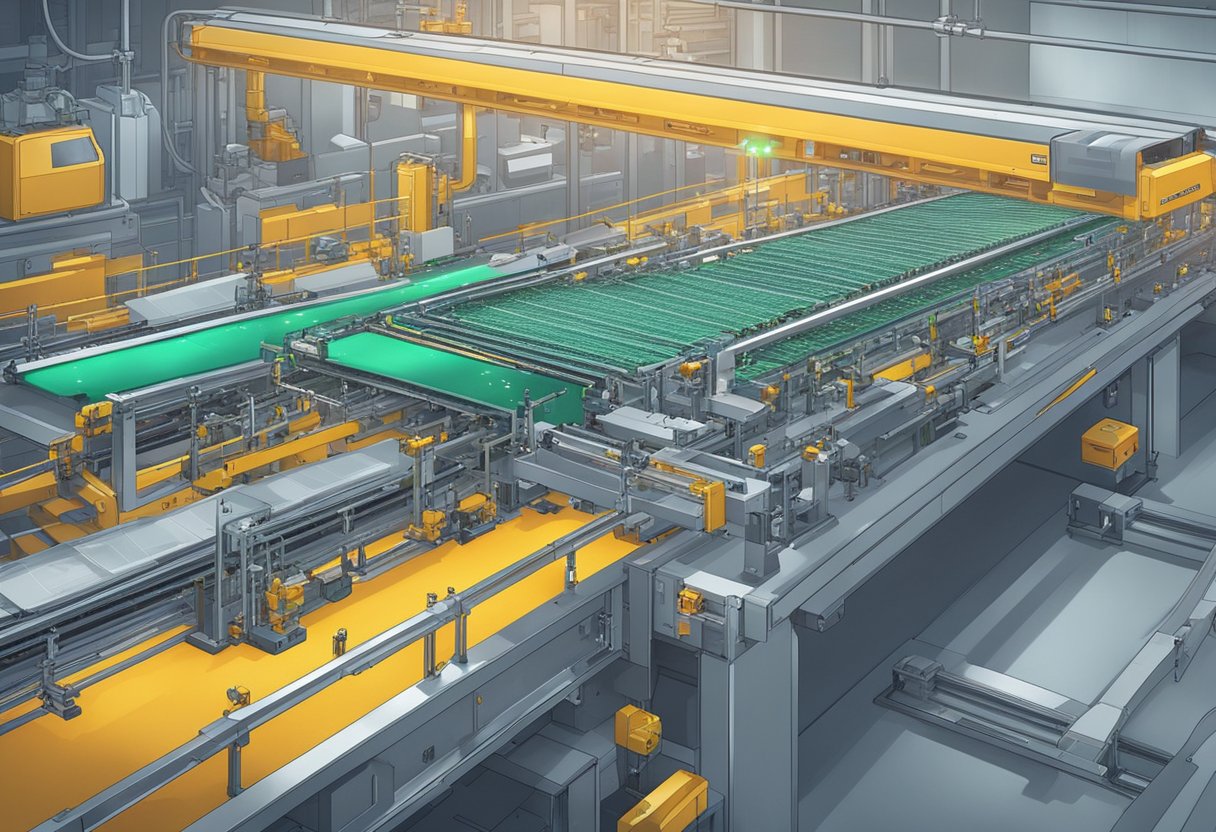
Fast turn PCB assembly is a process of manufacturing printed circuit boards (PCBs) in a quick and efficient manner. This process is ideal for companies that require a quick turnaround time for their PCBs. Fast turn PCB assembly involves a combination of automated and manual processes to ensure that the PCBs are manufactured accurately and quickly.
One of the key advantages of fast turn PCB assembly is the ability to reduce lead times. This is achieved by optimizing the manufacturing process and utilizing advanced machinery and equipment. Fast turn PCB assembly also helps to reduce costs by minimizing material waste and maximizing efficiency.
To achieve fast turn PCB assembly, companies typically use a variety of techniques such as automated optical inspection (AOI), surface mount technology (SMT), and through-hole technology (THT). These techniques help to ensure that the PCBs are manufactured to the highest quality standards and are free from defects.
Fast turn PCB assembly is particularly useful for companies that require a quick turnaround time for prototypes or low-volume production runs. This process can help to reduce the time and cost associated with traditional PCB manufacturing methods, while still maintaining high-quality standards.
Overall, fast turn PCB assembly is a reliable and efficient process that can help companies to meet their production deadlines and reduce costs. By utilizing advanced manufacturing techniques and equipment, companies can ensure that their PCBs are manufactured quickly and accurately, while still maintaining the highest quality standards.
Benefits of Fast Turn PCB Assembly
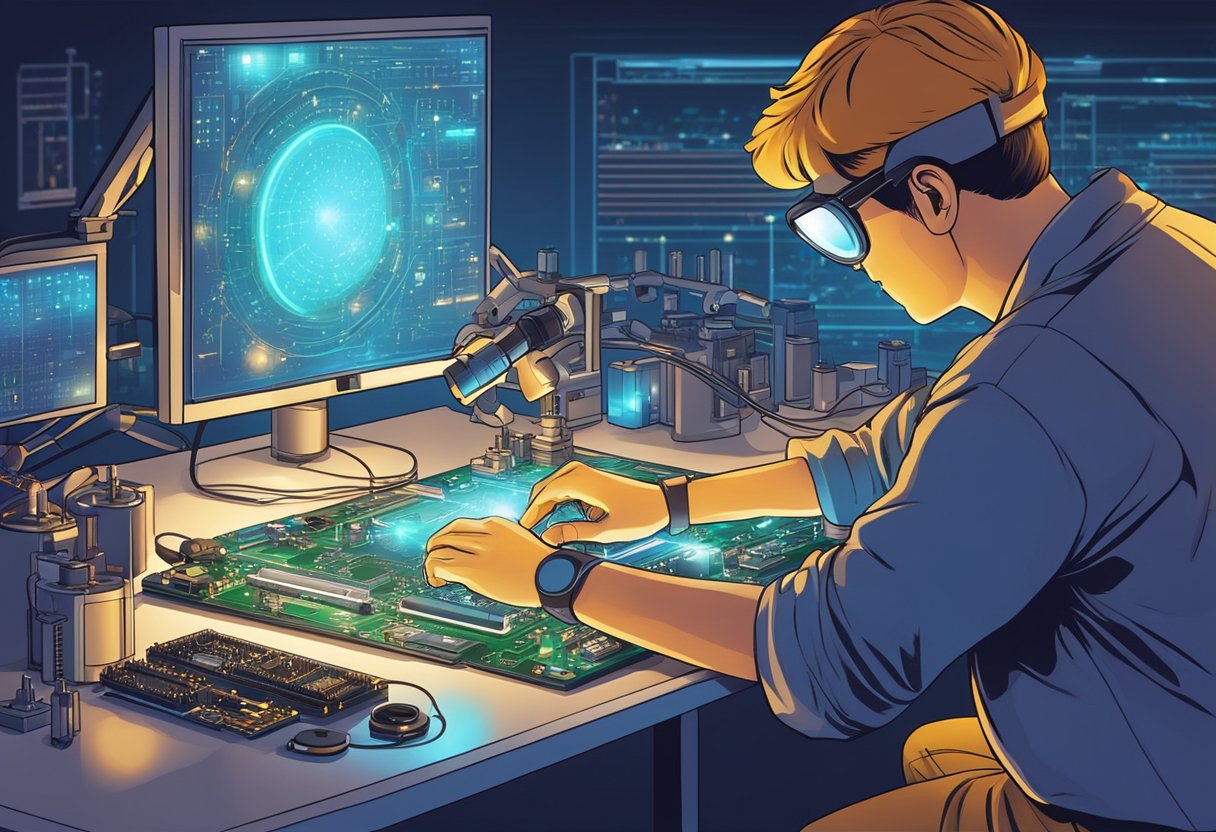
Fast turn PCB assembly offers several benefits that can help businesses meet their production goals while reducing costs and minimizing risks. This section will explore some of the key benefits of fast turn PCB assembly, including time efficiency, rapid prototyping, and market responsiveness.
Time Efficiency
One of the most significant benefits of fast turn PCB assembly is its time efficiency. With quick turnaround times, businesses can get their products to market faster, which can be critical in today’s competitive landscape. Fast turn PCB assembly allows businesses to reduce lead times, increase production speed, and improve overall efficiency. This can help businesses stay ahead of the competition and meet customer demands.
Rapid Prototyping
Fast turn PCB assembly also makes rapid prototyping possible. With the ability to quickly produce prototypes, businesses can test and refine their designs before committing to full-scale production. This can help reduce the risk of costly errors and ensure that the final product meets customer requirements. Rapid prototyping also allows businesses to explore new ideas and experiment with different designs, which can lead to innovation and improved products.
Market Responsiveness
Finally, fast turn PCB assembly enables businesses to be more responsive to market demands. With the ability to quickly produce and deliver products, businesses can respond to changing market conditions and customer needs. This can help businesses stay competitive and maintain their market share. Fast turn PCB assembly also allows businesses to take advantage of new opportunities and capitalize on emerging trends.
In conclusion, fast turn PCB assembly offers businesses several key benefits, including time efficiency, rapid prototyping, and market responsiveness. By leveraging these benefits, businesses can improve their production processes, reduce costs, and stay ahead of the competition.
Key Components of Fast Turn PCB Assembly
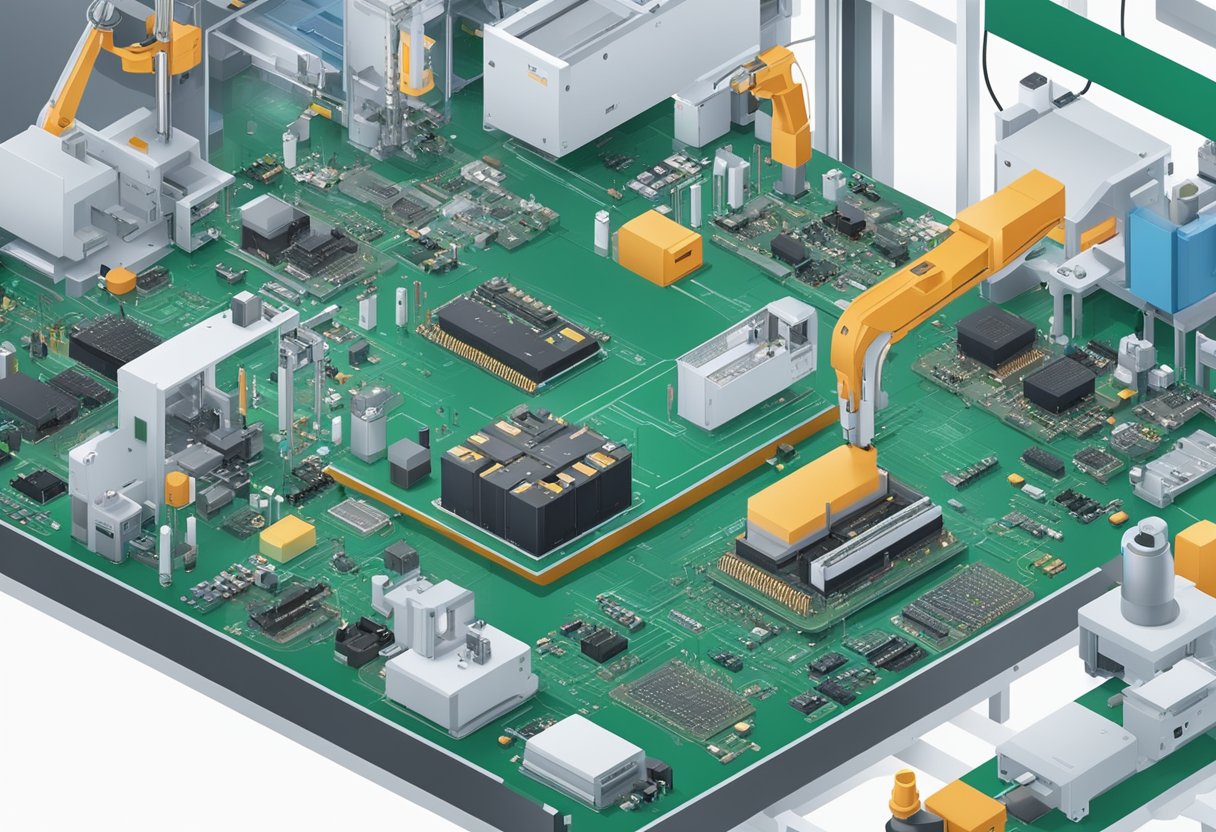
Fast turn PCB assembly is an essential aspect of modern-day electronics manufacturing. The process involves the rapid production of printed circuit boards (PCBs) to meet the growing demand for electronic devices. The following are key components of fast turn PCB assembly.
Material Selection
The selection of materials is crucial in the fast turn PCB assembly process. The use of high-quality materials ensures the durability and reliability of the PCBs. The materials used in the process include copper, FR-4, and solder mask. Copper is used for the conductive traces, while FR-4 is used as the substrate material. Solder mask is used to protect the PCB from external elements.
Manufacturing Equipment
Fast turn PCB assembly requires specialized equipment to ensure the quick and efficient production of PCBs. The equipment used in the process includes automated pick-and-place machines, stencil printers, reflow ovens, and inspection systems. The automated pick-and-place machines are used to place components on the PCBs, while stencil printers are used to apply solder paste to the PCBs. Reflow ovens are used to melt the solder paste and bond the components to the PCBs. Inspection systems are used to ensure the quality of the final product.
Quality Control
Quality control is a critical component of fast turn PCB assembly. The process involves the inspection of the PCBs at various stages of production to ensure that they meet the required standards. The inspection process includes visual inspection, automated optical inspection (AOI), and X-ray inspection. Visual inspection is carried out to detect any defects that may be visible to the naked eye. AOI is used to detect defects that may not be visible to the naked eye, while X-ray inspection is used to inspect the internal structure of the PCBs.
In conclusion, the key components of fast turn PCB assembly include material selection, manufacturing equipment, and quality control. The use of high-quality materials, specialized equipment, and rigorous quality control measures ensures the production of reliable and durable PCBs in a fast and efficient manner.
Design Considerations for Fast Turn PCBs
Fast turn PCB assembly requires careful consideration of the design and layout of the printed circuit board. Designers must focus on manufacturability and optimization to ensure that the PCB can be produced quickly without sacrificing quality. This section will explore two key design considerations for fast turn PCBs: design for manufacturability and layout optimization.
Design for Manufacturability
Design for manufacturability (DFM) is a critical consideration for fast turn PCB assembly. DFM involves designing the PCB with the manufacturing process in mind, ensuring that the board can be produced efficiently and with minimal errors. Some key DFM considerations include:
- Component selection: Choosing components that are readily available and easy to source can help speed up the assembly process.
- Footprint design: Designing footprints that are easy to place and solder can help reduce the risk of errors and speed up assembly.
- Trace width and spacing: Choosing appropriate trace widths and spacing can help ensure that the PCB can be produced without errors.
By focusing on DFM, designers can help ensure that their PCB can be produced quickly and with minimal errors.
Layout Optimization
Layout optimization is another key consideration for fast turn PCB assembly. Optimizing the layout can help reduce the time and cost of assembly, while also improving the performance of the PCB. Some key layout optimization considerations include:
- Component placement: Placing components in an optimal location can help reduce the length of traces and improve signal integrity.
- Routing: Careful routing can help ensure that the PCB can be produced quickly and with minimal errors.
- Layer count: Reducing the number of layers in the PCB can help reduce the time and cost of assembly.
By optimizing the layout of the PCB, designers can help ensure that their PCB can be produced quickly and with minimal errors, while also improving performance.
Ordering Process for Fast Turn PCBs
Fast turn PCB assembly is a critical service for many businesses that require quick turnaround times for their electronic products. The ordering process for fast turn PCBs is designed to be efficient and straightforward, enabling customers to receive their PCBs within a short time frame. This section outlines the steps involved in the ordering process for fast turn PCBs.
Quote and Cost Estimation
The first step in the ordering process for fast turn PCBs is to obtain a quote and cost estimation from the PCB manufacturer. Customers can submit their design files, and the manufacturer will provide a quote based on the design specifications, quantity, and turnaround time required. The quote will include the cost of the PCBs, any additional services required, and shipping costs.
Order Submission
Once the customer has approved the quote and cost estimation, they can submit their order to the manufacturer. The order should include the design files, any special instructions, and the required turnaround time. The manufacturer will review the order and confirm that the design files are suitable for production.
Design Verification
Before production begins, the manufacturer will verify the design files to ensure that they are suitable for PCB assembly. This includes checking for errors, verifying the design specifications, and ensuring that the design is manufacturable. If any issues are identified, the manufacturer will work with the customer to resolve them before production begins.
In conclusion, the ordering process for fast turn PCBs is designed to be efficient and straightforward, enabling customers to receive their PCBs within a short time frame. By following the steps outlined above, customers can ensure that their PCBs are produced accurately and delivered on time.
Manufacturing Process
PCB Fabrication
The first step in the fast turn PCB assembly process is the fabrication of the printed circuit board (PCB). This involves the creation of a board with the desired dimensions and electrical properties. The PCB fabrication process typically involves the following steps:
- Designing the PCB layout using computer-aided design (CAD) software
- Printing the layout onto a copper-clad board
- Etching the board to remove unwanted copper and leave the desired traces and pads
- Drilling holes for component leads and vias
- Plating the holes with copper to ensure electrical connectivity
- Applying a solder mask to protect the copper and facilitate soldering
- Adding a silkscreen layer for component labeling and identification
Component Assembly
Once the PCB is fabricated, the next step is to assemble the components onto the board. This involves placing the components onto the board and soldering them in place. Fast turn PCB assembly typically uses automated pick-and-place machines to place the components quickly and accurately. The soldering process can be done either manually or through a reflow oven, depending on the specific requirements of the project.
Testing and Inspection
After the components are assembled, the PCB undergoes testing and inspection to ensure that it meets the required specifications. This involves a range of tests, including:
- Electrical testing to check for proper connectivity and functionality
- Visual inspection to check for any defects or errors in the assembly process
- X-ray inspection to check for hidden defects or errors in the soldering process
By following a rigorous testing and inspection process, fast turn PCB assembly providers can ensure that their products meet the highest quality standards and are ready for use in a wide range of applications.