Streamlining Power Conversion with Bridge Rectifier PCB Layout
Bridge rectifiers play an imperative part in transforming alternating current (AC) into direct current (DC) when discussing power electronics. These devices are vital for providing the constant flow of power necessary to run electrical systems and hardware. A well-designed bridge rectifier PCB layout is essential for optimal performance and efficiency. In this blog post, we will explore the requirements and considerations involved in creating an efficient bridge rectifier PCB layout, with a focus on the expertise of Winow New Energy Company, a prominent manufacturer in the field.
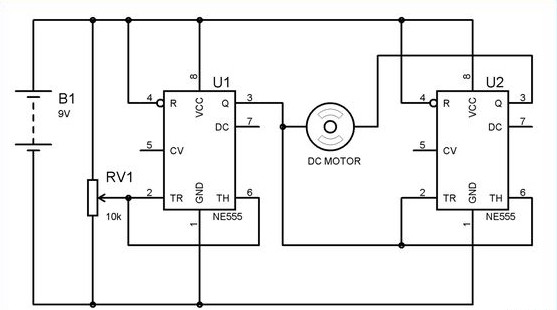
I. Importance of a Well-Designed Bridge Rectifier PCB Layout
1. Enhancing Efficiency:
Efficiency is a key factor in power conversion applications. A carefully crafted bridge rectifier PCB layout minimizes power losses and maximizes conversion efficiency. By reducing resistive losses, optimizing component placement, and employing appropriate trace widths, a well-designed layout can significantly enhance overall system efficiency.
2. Ensuring Reliability:
Reliability is of utmost importance in power electronics. A thoughtfully planned PCB layout ensures adequate thermal dissipation, minimizing the risk of component overheating and failure. Proper isolation techniques, such as maintaining appropriate creepage and clearance distances, also help ensure reliability and prevent electrical breakdown.
II. Requirements for a Bridge Rectifier PCB Layout
1. Component Placement:
Efficient component placement is critical for optimal performance. Placing the diodes, capacitors, and other components in close proximity reduces parasitic inductance and capacitance, minimizing voltage spikes and improving transient response. Winow New Energy Company focuses on careful component placement to achieve the desired electrical characteristics and enhance the overall performance of the bridge rectifier circuit.
2. Trace Routing and Layout Considerations:
Effective trace routing is essential for minimizing losses and ensuring efficient power delivery. Thick traces should be used for high-current paths, reducing resistance and voltage drops. Adequate spacing between traces, especially those carrying high voltages, prevents arcing and electrical breakdown. Winow New Energy Company’s expertise lies in designing optimized trace layouts that ensure reliable power delivery while minimizing electromagnetic interference (EMI) and crosstalk.
3. Thermal Management:
Heat dissipation is a critical aspect of power electronics design. Bridge rectifiers can generate significant heat during operation. A well-designed PCB layout incorporates thermal vias, heatsinks, and appropriate copper pour areas to efficiently transfer heat away from sensitive components. Winow New Energy Company’s expertise in thermal management techniques ensures that their bridge rectifier PCB layouts are optimized for heat dissipation, enhancing overall reliability and extending the lifespan of the components.
III. Winow New Energy Company: A Leader in Bridge Rectifier PCB Layout
1. Experience and Expertise:
Winow New Energy Company boasts years of experience in the power electronics industry. Their team of skilled engineers has a deep understanding of bridge rectifier circuit design and layout considerations. By leveraging their expertise, they can create customized PCB layouts that meet specific customer requirements, ensuring superior performance and reliability.
2. Advanced Design Tools and Testing:
Winow New Energy Company utilizes cutting-edge design tools and simulation software to optimize its bridge rectifier PCB layouts. Through thorough testing and analysis, they validate the design’s performance, identifying potential issues and refining the layout to achieve optimal results. This meticulous approach ensures that their bridge rectifier PCB layouts consistently meet the highest standards of quality and performance.
3. Customer-Centric Approach:
Winow New Energy Company takes a customer-centric approach, actively collaborating with clients to understand their unique needs and tailor the bridge rectifier PCB layout accordingly. By fostering open communication and providing responsive support, they strive to deliver solutions that align precisely with customer expectations and specifications.
Ⅳ. Designing Bridge Rectifier PCB Layout for High Power Applications: Challenges and Solutions
Designing a bridge rectifier printed circuit board (PCB) layout for high-power applications requires careful consideration of various factors to ensure optimal performance and reliability. As the demand for efficient power conversion continues to rise, manufacturers like Winow New Energy Company are faced with the challenge of designing robust and efficient PCB layouts that can handle high power levels.
1. Thermal Management: Keeping Temperatures in Check
In high-power applications, one of the significant challenges is managing the heat generated by the bridge rectifier circuit. The power dissipated by the rectifier diodes can lead to a temperature rise, potentially affecting the overall performance and reliability of the system. To address this issue, the PCB layout must incorporate proper thermal management techniques such as heat sinks, thermal vias, and copper planes to dissipate heat efficiently and maintain acceptable operating temperatures.
2. High Voltage Traces and Clearances: Ensuring Safety
Another critical aspect of designing a bridge rectifier PCB layout for high-power applications is maintaining appropriate voltage traces and clearances. High-voltage lines carry a significant risk of electrical arcing, especially when the clearance distances between traces are insufficient. To ensure safety, it is essential to adhere to the relevant safety standards and design guidelines, such as maintaining adequate creepage and clearance distances, using suitable insulation materials, and incorporating isolation barriers as necessary.
3. Proper Component Placement and Routing: Minimizing Inductive Effects
High-power applications often involve considerable current flow, which can induce inductive effects on nearby traces and components. To mitigate these effects, careful consideration must be given to component placement and routing techniques. Placing components strategically and minimizing loop areas can help reduce inductance and improve overall system efficiency.
4. Board Layout Considerations: Minimizing Parasitic Capacitance
Parasitic capacitance is a common challenge in high-power PCB designs and can negatively impact circuit performance. Minimizing the parasitic capacitance between traces and components is crucial for reducing the potential for unintended coupling, signal degradation, or electromagnetic interference. Appropriate spacing, shielding, and proper ground plane design can help minimize parasitic capacitance and optimize the overall performance of the bridge rectifier circuit.
Conclusion:
A well-designed bridge rectifier PCB layout is fundamental for efficient power conversion, reliability, and longevity of power electronics systems. Winow New Energy Company’s expertise in bridge rectifier PCB layout design, coupled with their commitment to delivering high-quality solutions, makes them a trusted manufacturer in the field. By leveraging their experience, advanced design tools, and customer-centric approach, Winow New Energy Company consistently provides optimized bridge rectifier PCB layouts that empower power electronics systems with exceptional performance and reliability.