Aerospace PCB Assembly: Key Considerations for High-Reliability Systems
Aerospace PCB assembly is a critical process in the manufacturing of aerospace and defense equipment. The assembly of printed circuit boards (PCBs) for aerospace applications requires a high level of precision and attention to detail. These PCBs are used in a variety of aerospace and defense applications, including satellites, missiles, and aircraft.
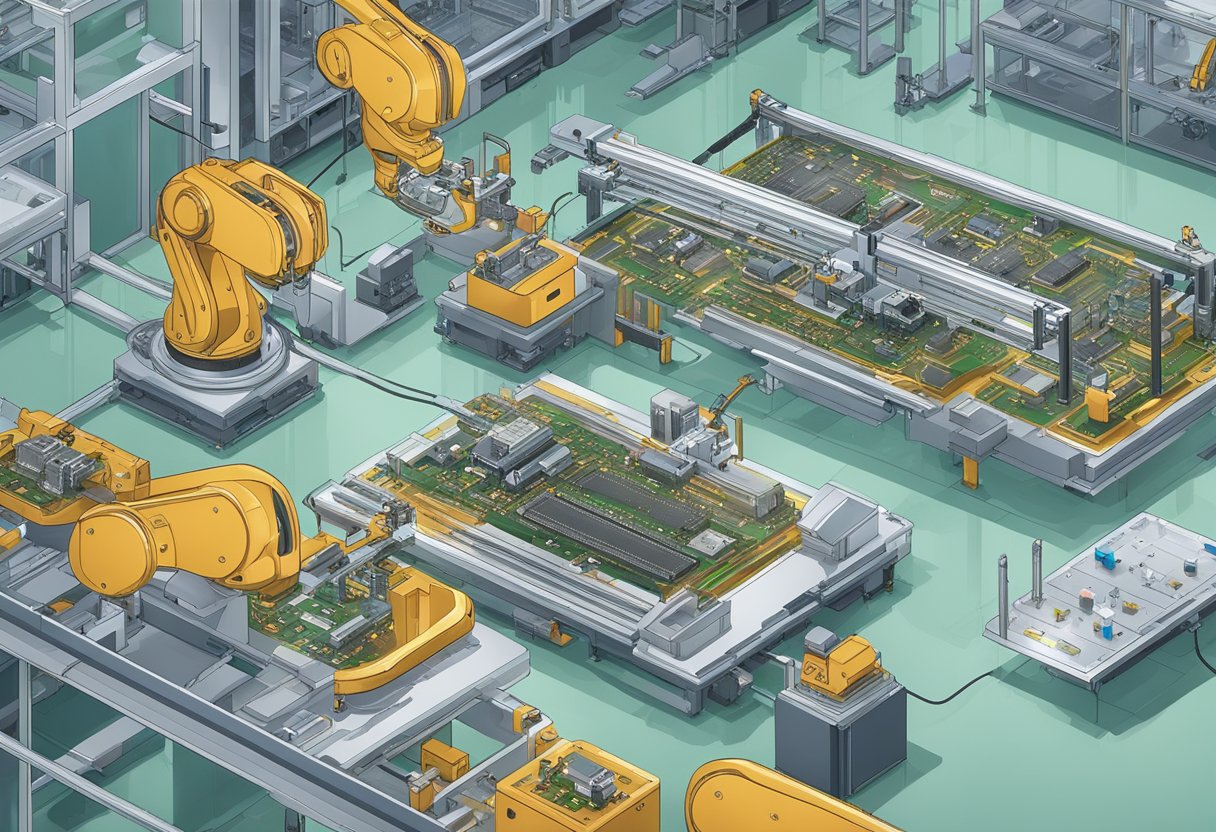
The requirements for aerospace PCB assembly are stringent and demanding. The PCBs used in aerospace applications must be designed to withstand extreme temperatures, vibrations, and other environmental factors. They must also be able to operate in harsh conditions, such as high altitude, radiation, and electromagnetic interference. As a result, the materials and components used in aerospace PCB assembly must be of the highest quality and reliability.
Overview of Aerospace PCB Assembly
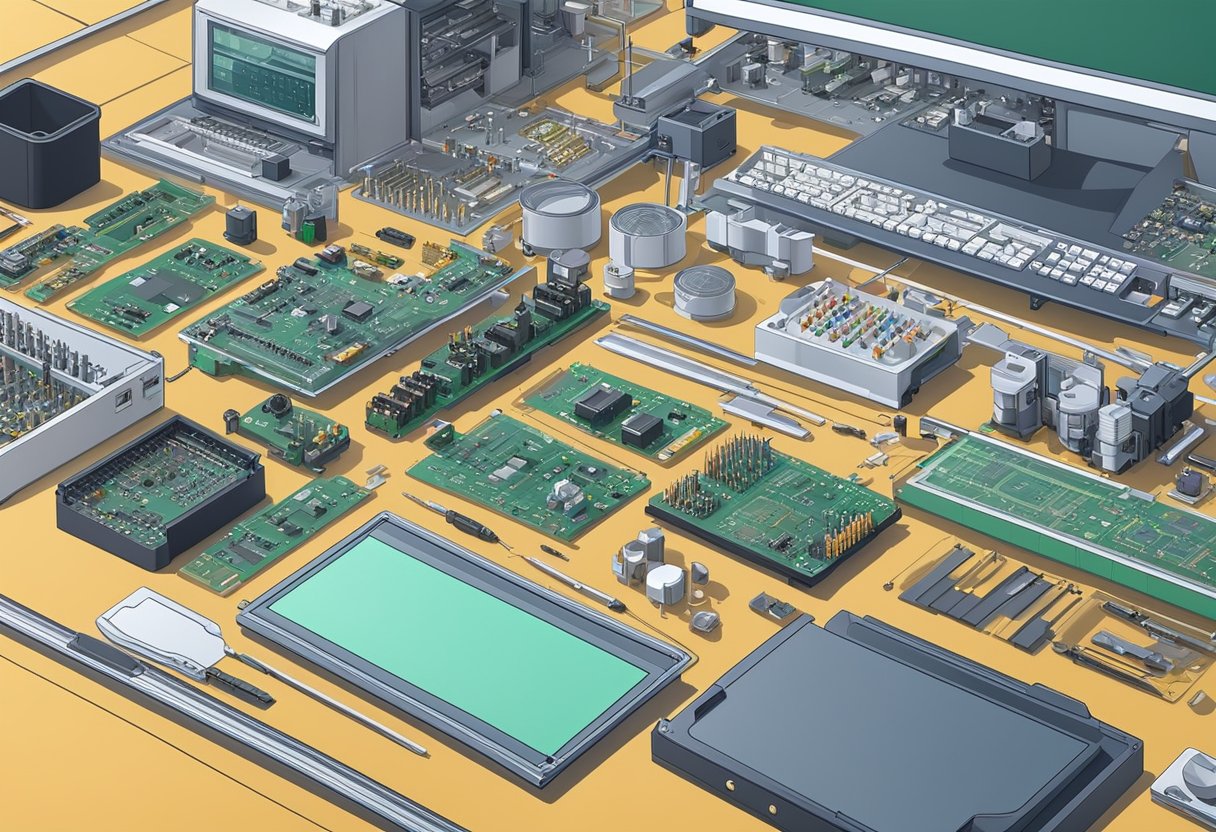
Aerospace PCB assembly is a critical process in the manufacturing of aerospace equipment. Printed circuit boards (PCBs) are used in a wide range of aerospace applications, including flight control systems, communication systems, and navigation systems.
The assembly of aerospace PCBs requires a high degree of precision and accuracy to ensure that the final product meets the strict quality and safety standards required for use in the aerospace industry. This is because any failure or malfunction of the PCB could have serious consequences, including loss of life or damage to property.
To ensure the highest level of quality and reliability, aerospace PCBs are assembled using specialized equipment and techniques. These include automated assembly machines, surface mount technology (SMT), and through-hole technology (THT).
In addition to the use of specialized equipment, aerospace PCB assembly also requires strict adherence to industry standards and regulations. This includes compliance with the International Traffic in Arms Regulations (ITAR), which govern the export and import of defense-related articles and services.
Overall, aerospace PCB assembly is a complex and highly specialized process that requires a combination of technical expertise, advanced equipment, and strict quality control measures to ensure the highest level of safety and reliability in aerospace applications.
Materials and Components
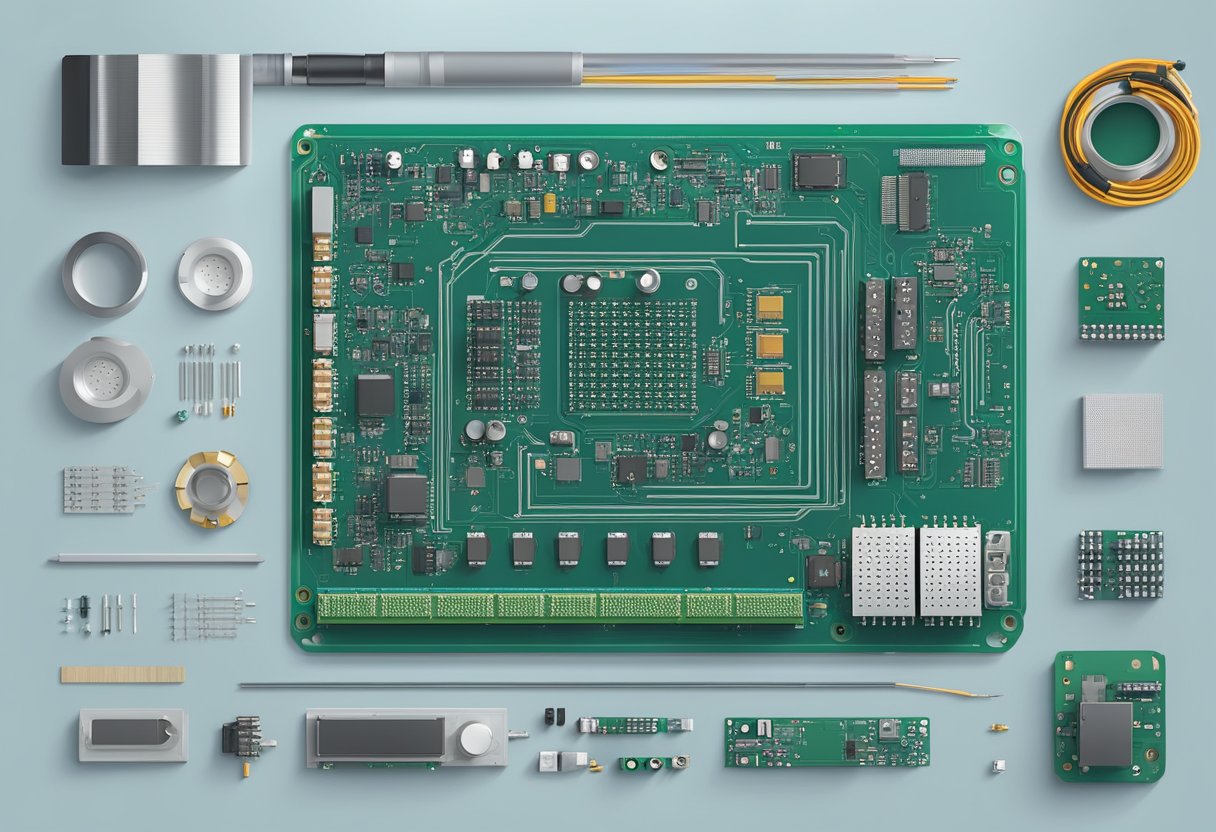
PCB Materials
The materials used for aerospace PCB assembly must be able to withstand harsh environmental conditions such as extreme temperatures, vibrations, and radiation. The most commonly used materials for aerospace PCBs are high-temperature laminates, such as polyimide and ceramic-filled PTFE. These materials have a high glass transition temperature, which allows them to maintain their structural integrity at high temperatures.
Electronic Components
Electronic components used in aerospace PCB assembly must also be able to withstand harsh environmental conditions. Components with a high tolerance for temperature, vibration, and radiation are preferred. Ceramic capacitors, tantalum capacitors, and surface-mount resistors are commonly used in aerospace applications due to their high reliability and ability to withstand harsh conditions.
Surface Finishes
The surface finish of a PCB is critical for ensuring proper soldering and long-term reliability. In aerospace applications, the most commonly used surface finishes are immersion gold and electroless nickel immersion gold (ENIG). These finishes provide excellent solderability and corrosion resistance, which are essential for the harsh environments encountered in aerospace applications.
In summary, the materials and components used in aerospace PCB assembly must be carefully selected to ensure that they can withstand harsh environmental conditions. High-temperature laminates, ceramic capacitors, tantalum capacitors, and surface-mount resistors are commonly used in aerospace applications. Immersion gold and ENIG are the most commonly used surface finishes for aerospace PCBs.
Design Considerations
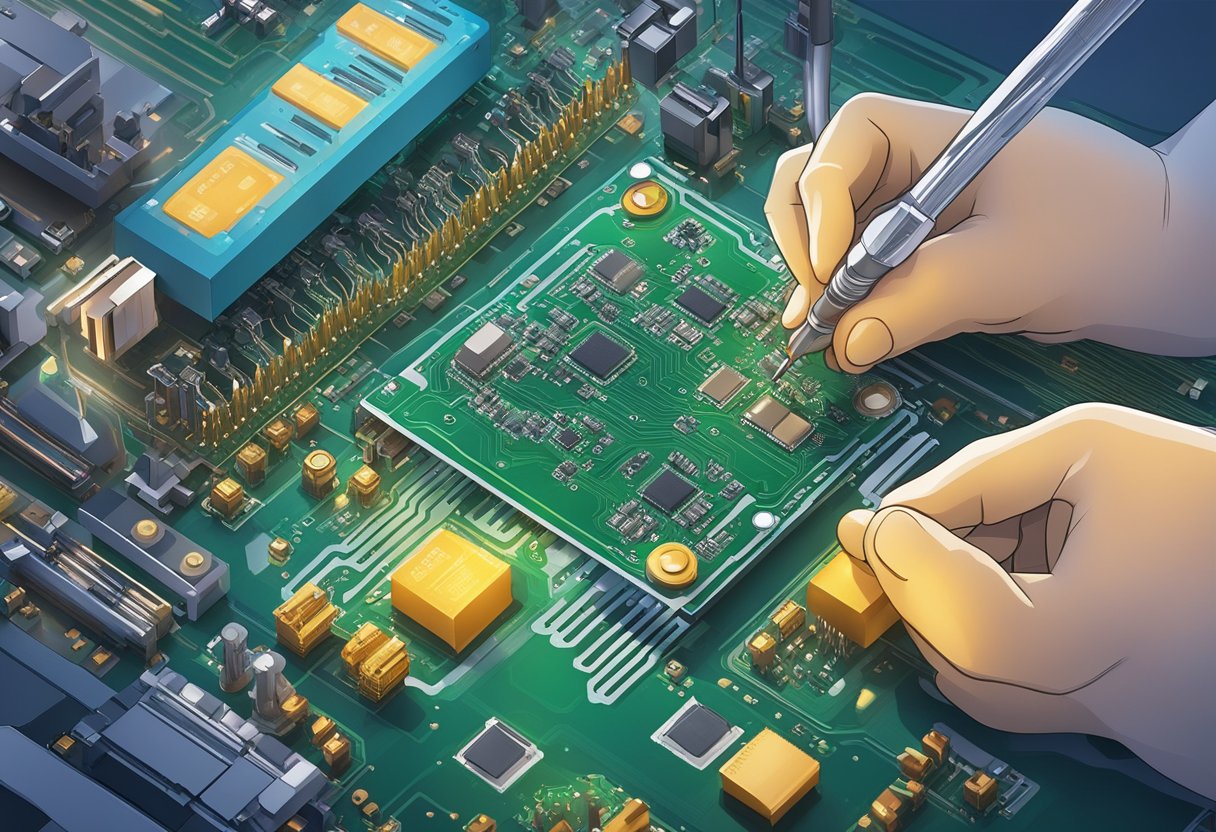
When designing aerospace PCB assemblies, there are several crucial considerations that engineers must take into account to ensure that the final product meets the required specifications. The following subsections outline some of the essential design considerations for aerospace PCB assembly.
Thermal Management
In aerospace applications, PCBs must operate reliably under extreme temperature conditions. Therefore, thermal management is a critical consideration when designing aerospace PCB assemblies. Engineers must ensure that the PCB design includes adequate heat sinking and thermal vias to dissipate heat effectively. Additionally, the PCB substrate material should have a low coefficient of thermal expansion to minimize the risk of thermal stress-induced failure.
Signal Integrity
Signal integrity is another crucial consideration when designing aerospace PCB assemblies. High-speed digital signals and RF signals are common in aerospace applications, and any signal distortion or noise can cause significant problems. Engineers must ensure that the PCB layout and routing minimize signal loss, crosstalk, and electromagnetic interference (EMI). Additionally, the use of controlled impedance traces and differential signaling can improve signal integrity.
Mechanical Constraints
Aerospace PCB assemblies must also meet strict mechanical requirements. The PCB must fit within the available space and withstand the mechanical stresses and vibrations associated with launch, operation, and landing. Engineers must consider the PCB’s mounting and attachment methods, as well as the use of stiffeners and shock absorbers, to ensure that the PCB can withstand the mechanical stresses of the application.
In summary, thermal management, signal integrity, and mechanical constraints are critical design considerations for aerospace PCB assemblies. Engineers must carefully consider these factors to ensure that the final product meets the required specifications and can operate reliably in the harsh conditions of aerospace applications.
Manufacturing Processes
Soldering Techniques
One of the critical steps in aerospace PCB assembly is the soldering process. Soldering is the process of joining two metal surfaces with a third metal that has a lower melting point than the two surfaces being joined. There are several soldering techniques used in aerospace PCB assembly, such as wave soldering, reflow soldering, and hand soldering.
Wave soldering is a popular soldering technique used in PCB assembly. It involves passing the PCB over a wave of molten solder to solder the components to the PCB. Reflow soldering is another technique that involves melting the solder paste applied to the PCB using a hot air or infrared source. Hand soldering is a manual process that involves using a soldering iron and solder wire to join the components to the PCB.
Automated Assembly
Automated assembly is a critical process in aerospace PCB assembly. It involves using machines and robots to place components on the PCB. Automated assembly is faster and more accurate than manual assembly, and it reduces the risk of errors caused by human factors.
Automated assembly machines use a variety of techniques to place components on the PCB, such as pick-and-place machines, screen printers, and dispensers. Pick-and-place machines use a vacuum to pick up components and place them on the PCB. Screen printers apply solder paste to the PCB, and dispensers apply adhesives and other materials to the PCB.
Quality Control
Quality control is an essential aspect of aerospace PCB assembly. It ensures that the PCB meets the required standards and specifications. Quality control involves several processes, such as inspection, testing, and verification.
Inspection involves visually inspecting the PCB to ensure that it meets the required standards. Testing involves testing the PCB to ensure that it functions correctly. Verification involves verifying that the PCB meets the required specifications and standards.
In conclusion, aerospace PCB assembly involves several critical processes, such as soldering, automated assembly, and quality control. These processes must be performed with precision and accuracy to ensure that the PCB meets the required standards and specifications.
Testing and Certification
Aerospace PCB assembly requires rigorous testing and certification to ensure that the final product meets industry standards and is safe for use in aircraft. The testing process involves several stages, including functional testing, environmental testing, and compliance with industry standards.
Functional Testing
Functional testing is a critical stage in the assembly process, where the assembled PCB is tested to ensure that it performs as intended. This involves checking the functionality of individual components, such as resistors, capacitors, and diodes, as well as the overall performance of the PCB. The testing process can be automated, using specialized software and equipment, or conducted manually, depending on the complexity of the assembly.
Environmental Testing
Environmental testing is another crucial stage in the assembly process, where the PCB is subjected to extreme conditions to simulate the harsh environments it may encounter during its lifetime. This includes testing for temperature, humidity, vibration, and shock resistance. The testing process ensures that the PCB can withstand these conditions without failure or degradation in performance.
Industry Standards
Compliance with industry standards is essential for aerospace PCB assembly. The industry standards ensure that the final product meets the required safety and performance standards. The most commonly used industry standards for aerospace PCB assembly include the IPC-A-610 and IPC-6012. These standards cover everything from design and materials to assembly and testing.
In conclusion, testing and certification are critical stages in aerospace PCB assembly. The rigorous testing process ensures that the final product meets industry standards and is safe for use in aircraft. Compliance with industry standards is essential for ensuring the safety and performance of the final product.
Reliability and Durability
Lifetime Expectancy
Aerospace PCB assembly requires high reliability and durability to ensure the safety and success of missions. The lifetime expectancy of aerospace PCBs is a critical factor in determining their suitability for use in aerospace applications.
PCBs used in aerospace applications must be designed and manufactured to withstand extreme conditions such as temperature changes, vibrations, and shocks. The lifetime expectancy of these PCBs depends on several factors, including the quality of materials used, the manufacturing process, and the operating conditions.
PCBs designed for aerospace applications typically have a lifetime expectancy of 10 to 15 years. However, this can vary depending on the specific application and the conditions in which the PCB is used.
Failure Analysis
Despite the high reliability and durability of aerospace PCBs, failures can still occur. Failure analysis is a critical process used to determine the root cause of failures and prevent future failures from occurring.
When a failure occurs, the PCB is carefully analyzed to identify the cause of the failure. This involves examining the PCB’s design, materials, and manufacturing process to determine where the failure occurred and why.
Once the root cause of the failure has been identified, steps can be taken to prevent future failures. This may involve redesigning the PCB, changing the materials used, or modifying the manufacturing process.
In conclusion, reliability and durability are critical factors in aerospace PCB assembly. PCBs designed for aerospace applications must be able to withstand extreme conditions and have a lifetime expectancy of 10 to 15 years. Failure analysis is a critical process used to identify the root cause of failures and prevent future failures from occurring.