How to Leverage FMEA for PCB Assembly
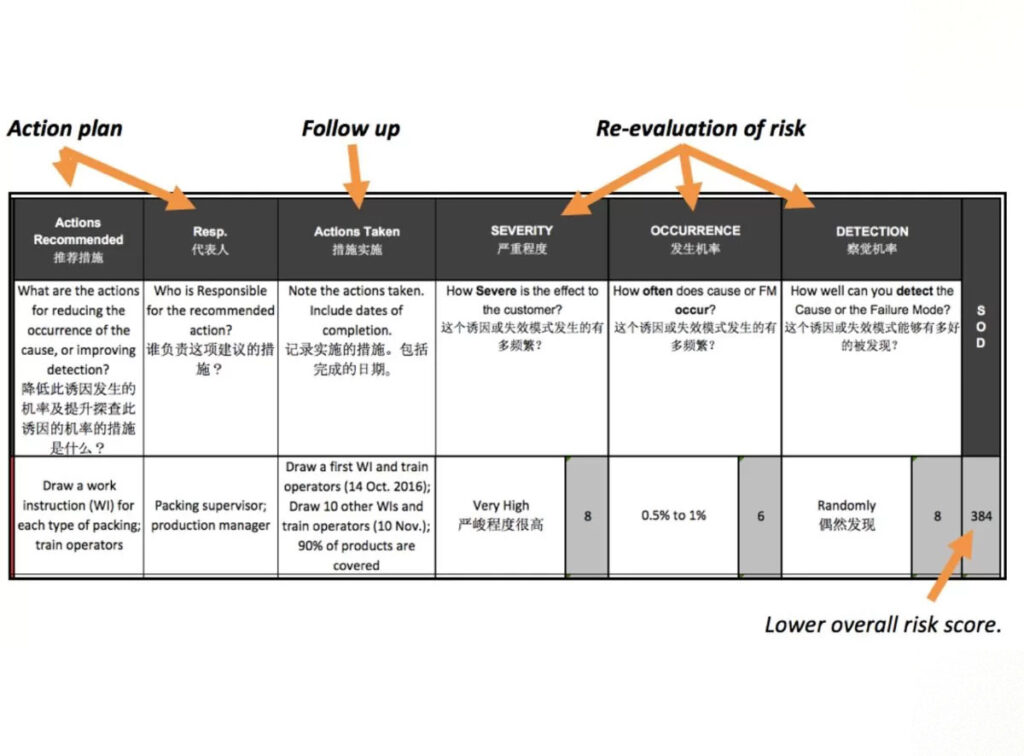
Failure Mode and Effect Analysis (FMEA) is a powerful tool used to identify, prioritize and mitigate risks in the PCB (Printed Circuit Board) assembly process. It is used to ensure that the quality and reliability of the PCB assembly meets the required standards. This blog will provide an overview of FMEA for PCB assembly, its benefits, components, and practical applications.
What is FMEA for PCB assembly?
FMEA for PCB assembly is a structured approach to identify and manage potential risks in the PCB assembly process. It is used to reduce the chance of failure in the assembly process by identifying and addressing potential problem areas before they become an issue. FMEA is a proactive approach to risk management, as it seeks to identify and address risks before they become problems.
The core of FMEA for PCB assembly is the Risk Priority Number (RPN), which is a numerical value used to prioritize risks and determine which risks should be addressed first. The RPN is calculated by multiplying the Severity, Occurrence, and Detection scores together. The higher the RPN score, the higher priority risk.
The purpose of FMEA for PCB assembly is to identify potential failure modes, prioritize risks, and develop effective risk mitigation strategies. FMEA is an invaluable tool for PCB assembly, as it helps identify potential issues and reduce the risk of costly failures.
Benefits of FMEA for PCB assembly
FMEA for PCB assembly provides a number of benefits, including:
- Improved product quality: FMEA helps to identify potential issues and risks early in the design process, allowing for the development of improved product quality.
- Reduced cost of assembly: FMEA can help to reduce the cost of PCB assembly by identifying and addressing potential problems before they become an issue.
- Improved reliability: FMEA helps to improve the reliability of the PCB assembly by identifying and addressing potential failures and risks.
- Increased customer satisfaction: FMEA helps to ensure that the product meets customer expectations, leading to increased customer satisfaction.
Understanding FMEA failure modes
FMEA for PCB assembly involves the identification of potential failure modes, which are the ways in which a product or process can fail. The failure modes can be categorized into three categories: design, process, and environmental.
Design related failure modes are related to the design of the PCB or its components. Process related failure modes are related to the manufacturing process and environmental failure modes are related to the environment in which the product is used.
Once the potential failure modes have been identified, it is important to assess the risks associated with each failure mode. This can be done by assigning a Severity, Occurrence, and Detection score to each failure mode.
Establishing FMEA risk assessment criteria
After the potential failure modes have been identified, it is important to establish the criteria for assessing the risks associated with each failure mode. This is done by assigning a Severity, Occurrence, and Detection score to each failure mode.
The Severity score is used to measure the potential consequences of the failure. The Occurrence score is used to measure the likelihood of the failure occurring. The Detection score is used to measure the effectiveness of existing methods for detecting the failure.
Once the Severity, Occurrence, and Detection scores have been assigned, the Risk Priority Number (RPN) is calculated by multiplying the three scores together. The higher the RPN score, the higher priority risk.
Conducting FMEA risk analysis
Once the RPN scores have been calculated, a risk analysis should be conducted to identify the highest priority risks and determine the best risk mitigation strategies.
The risk analysis should include an evaluation of the Severity, Occurrence, and Detection scores to determine the root cause of the risk. The risk analysis should also include an evaluation of the existing risk mitigation strategies to determine if they are effective. If the existing risk mitigation strategies are ineffective, new strategies should be developed.
Implementing FMEA risk mitigation strategies
Once the risk mitigation strategies have been identified, it is important to implement them to reduce the risk of failure. The implementation of the risk mitigation strategies should be monitored to ensure that they are effective.
The implementation of the risk mitigation strategies should also be documented to ensure that the strategies are properly implemented and maintained. The documentation should include the results of the risk analysis, the risk mitigation strategies, and the results of the implementation of the risk mitigation strategies.
Optimizing FMEA for PCB assembly
Once the risk mitigation strategies have been implemented, it is important to optimize the FMEA process for PCB assembly. This can be done by continually monitoring the performance of the FMEA process and making modifications as necessary.
The performance of the FMEA process should be monitored by tracking the RPN scores of the identified risks. If the RPN scores are not decreasing, modifications should be made to the FMEA process.
FMEA for PCB assembly tools and software
There are a number of tools and software available to help with the FMEA process for PCB assembly. These tools and software can be used to automate the FMEA process and make it easier to identify and prioritize risks.
The tools and software can also be used to track the performance of the FMEA process and make modifications as necessary. This helps to ensure that the FMEA process is optimized for maximum effectiveness.
FMEA for PCB assembly services
In addition to the tools and software available for FMEA for PCB assembly, there are also a number of services available to help with the FMEA process. These services can provide expert advice and guidance on the FMEA process, as well as helping to identify and prioritize risks.
The services can also help to implement and optimize the FMEA process for maximum effectiveness. They can also help to develop custom risk mitigation strategies to address specific risks and ensure that the FMEA process is optimized for PCB assembly.
Conclusion
FMEA for PCB assembly is a powerful tool for identifying, prioritizing, and mitigating risks in the PCB assembly process. It is used to reduce the chance of failure in the assembly process by identifying and addressing potential problem areas before they become an issue.
FMEA is an invaluable tool for PCB assembly, as it helps identify potential issues and reduce the risk of costly failures. It is also important to optimize the FMEA process for PCB assembly by continually monitoring the performance of the FMEA process and making modifications as necessary.
There are a number of tools and software available to help with the FMEA process for PCB assembly. There are also a number of services available to help with the FMEA process, such as providing expert advice and guidance, and helping to implement and optimize the FMEA process for maximum effectiveness.
Overall, FMEA for PCB assembly is an invaluable tool for reducing the risk of costly failures and ensuring that the PCB assembly meets customer expectations. If you are looking to reduce the risk of failure in your PCB assembly process, FMEA is a powerful tool to help you do so.