PCB Functional Test
PCB functional test is a method of testing printed circuit boards (PCBs) to ensure that they are functioning correctly and meet specified quality standards. It is typically used to identify and correct defects before the final product is assembled.
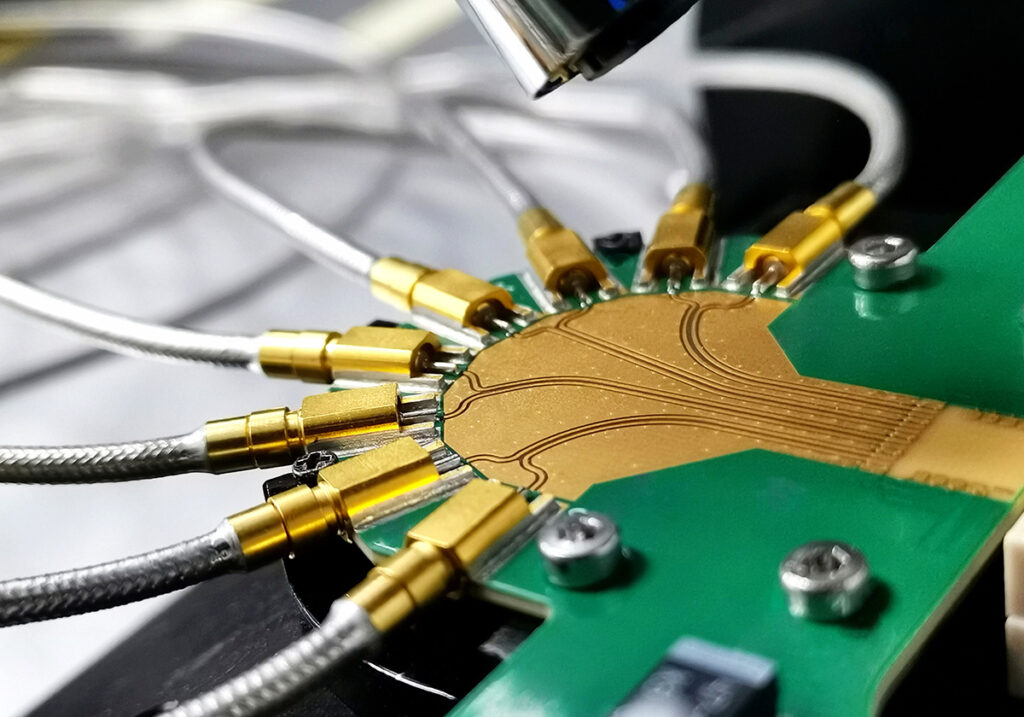
There are several types of functional tests that can be performed on PCBs, including:
- In-circuit test (ICT): ICT involves sending electrical signals through the PCB and measuring the responses. The test machine is programmed with the expected responses for each signal, and any deviations from the expected response are flagged as defects.
- Boundary scan test: Boundary scan test involves sending test signals through the boundary scan cells on the PCB and measuring the responses. It is used to test the connectivity and functionality of the PCB’s components.
- JTAG test: JTAG (Joint Test Action Group) test involves sending test signals through the JTAG port on the PCB and measuring the responses. It is used to test the functionality of the PCB’s components and debug any issues.
- Functional test: Functional test involves testing the PCB by simulating the actual use of the final product. It is used to ensure that the PCB functions correctly when it is incorporated into the final product.
There are several benefits to performing functional test on PCBs:
- Increased defect detection: Functional test can detect defects that may be difficult or impossible for a human tester to see, such as shorts or opens in circuit traces.
- Improved product quality: By identifying and correcting defects early in the manufacturing process, functional test can help improve the overall quality of the finished product.
- Reduced testing costs: Automated testing reduces the need for manual labor, which can significantly reduce testing costs.
However, there are also some limitations to functional test:
- Cost: Functional test equipment can be expensive to purchase and maintain.
- Dependence on test program: The accuracy of the test results depends on the accuracy of the test program, which must be carefully developed and maintained.
- Limited to functional testing: Functional test is typically limited to functional testing, and may not be able to detect physical defects such as scratches or dents.
PCB Functional Test FAQ
- What is PCB functional test?
PCB functional test is a method of testing printed circuit boards (PCBs) to ensure that they are functioning correctly and meet specified quality standards. It is typically used to identify and correct defects before the final product is assembled.
- What types of functional tests can be performed on PCBs?
There are several types of functional tests that can be performed on PCBs, including:
- In-circuit test (ICT): ICT involves sending electrical signals through the PCB and measuring the responses. The test machine is programmed with the expected responses for each signal, and any deviations from the expected response are flagged as defects.
- Boundary scan test: Boundary scan test involves sending test signals through the boundary scan cells on the PCB and measuring the responses. It is used to test the connectivity and functionality of the PCB’s components.
- JTAG test: JTAG (Joint Test Action Group) test involves sending test signals through the JTAG port on the PCB and measuring the responses. It is used to test the functionality of the PCB’s components and debug any issues.
- Functional test: Functional test involves testing the PCB by simulating the actual use of the final product. It is used to ensure that the PCB functions correctly when it is incorporated into the final product.
- What are the benefits of performing functional test on PCBs?
There are several benefits to performing functional test on PCBs:
- Increased defect detection: Functional test can detect defects that may be difficult or impossible for a human tester to see, such as shorts or opens in circuit traces.
- Improved product quality: By identifying and correcting defects early in the manufacturing process, functional test can help improve the overall quality of the finished product.
- Reduced testing costs: Automated testing reduces the need for manual labor, which can significantly reduce testing costs.
- What are the limitations of functional test?
There are a few limitations to functional test:
- Cost: Functional test equipment can be expensive to purchase and maintain.
- Dependence on test program: The accuracy of the test results depends on the accuracy of the test program, which must be carefully developed and maintained.
- Limited to functional testing: Functional test is typically limited to functional testing, and may not be able to detect physical defects such as scratches or dents.
- What types of products can be tested with functional test?
Functional test can be used to test a wide range of electronic components, including PCBs, microelectronic devices, and other electronic components. It is commonly used in the electronics manufacturing industry to test components before they are assembled into final products.